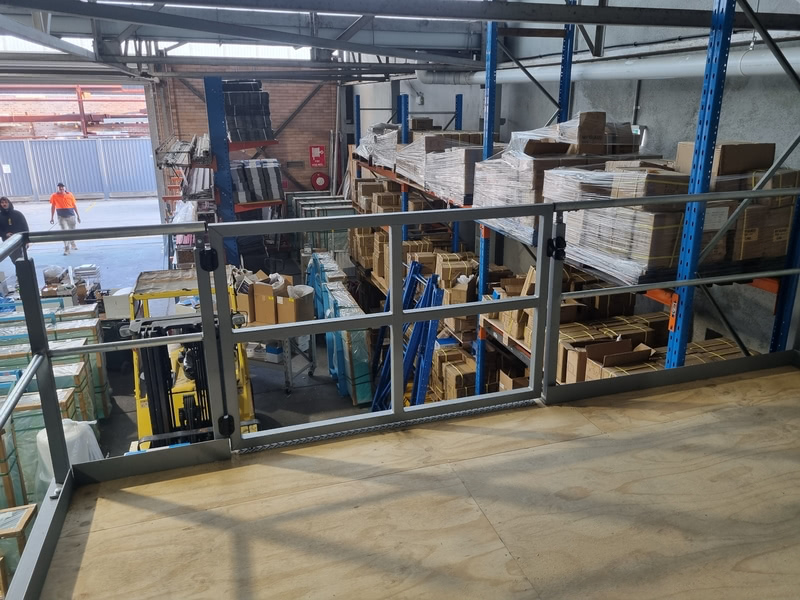
Gallery
Take a look at some of our past work and completed projects.
Mezzanine Floors
Tailored Project Group, Brisbane QLD
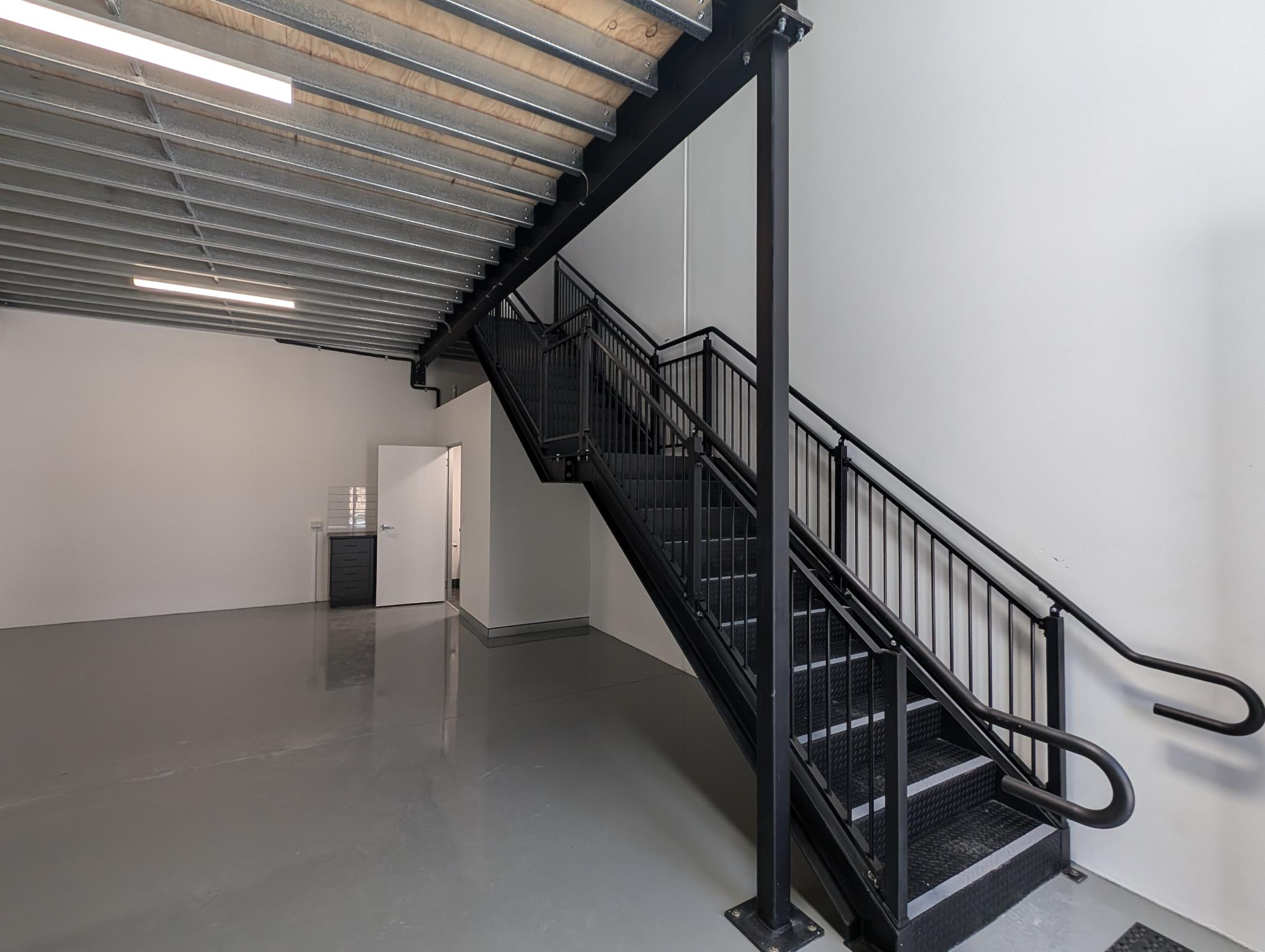
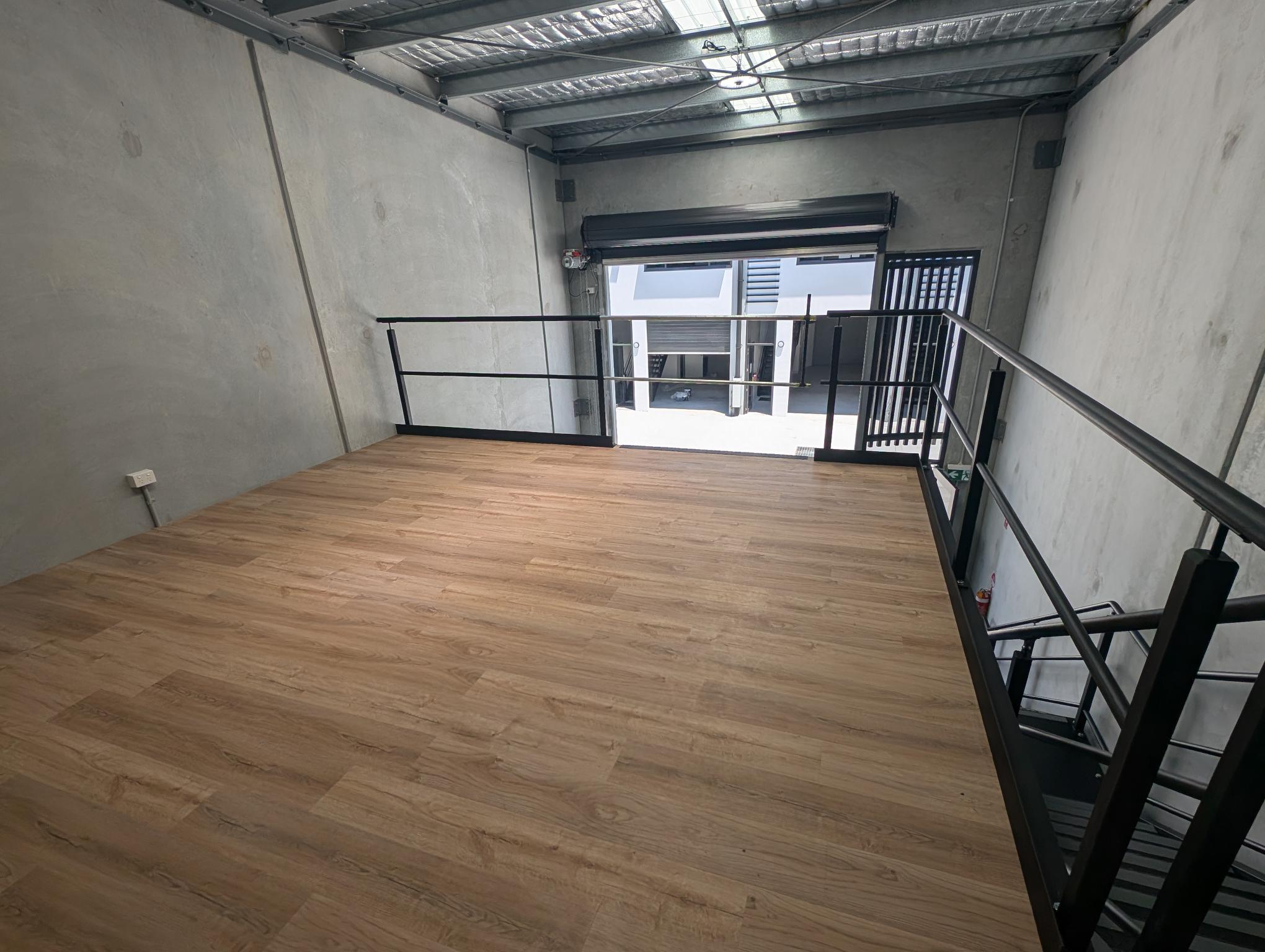
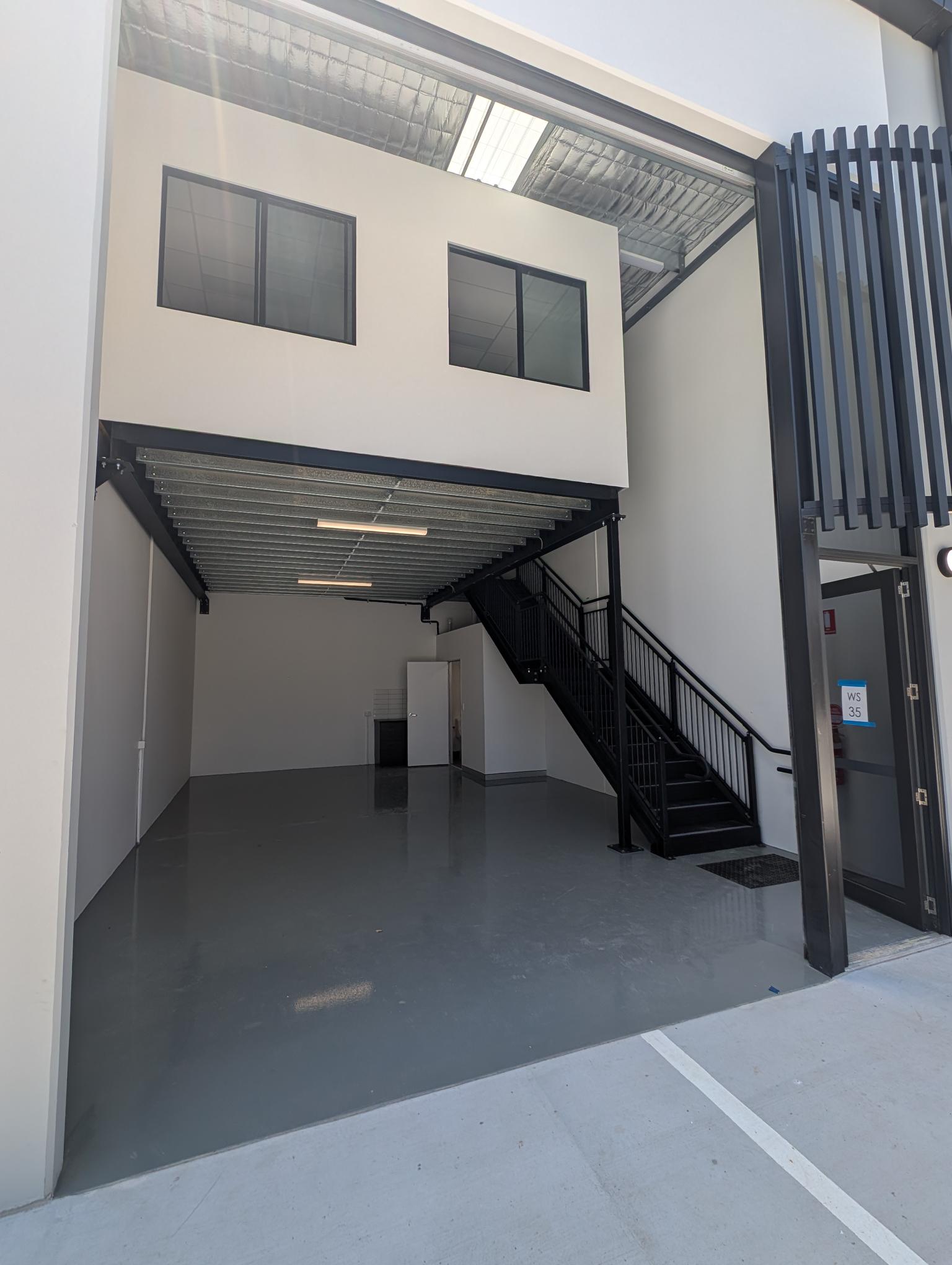
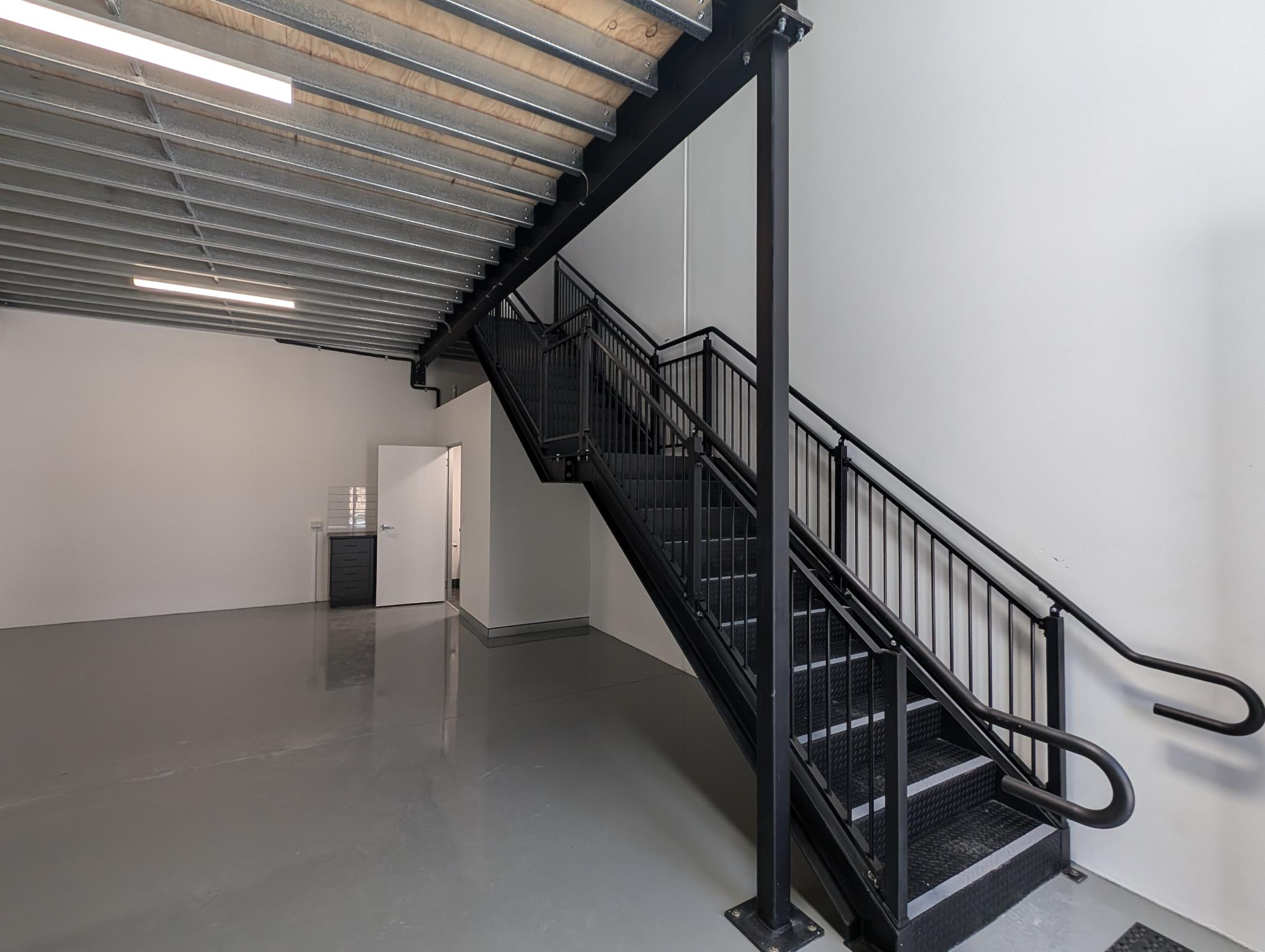
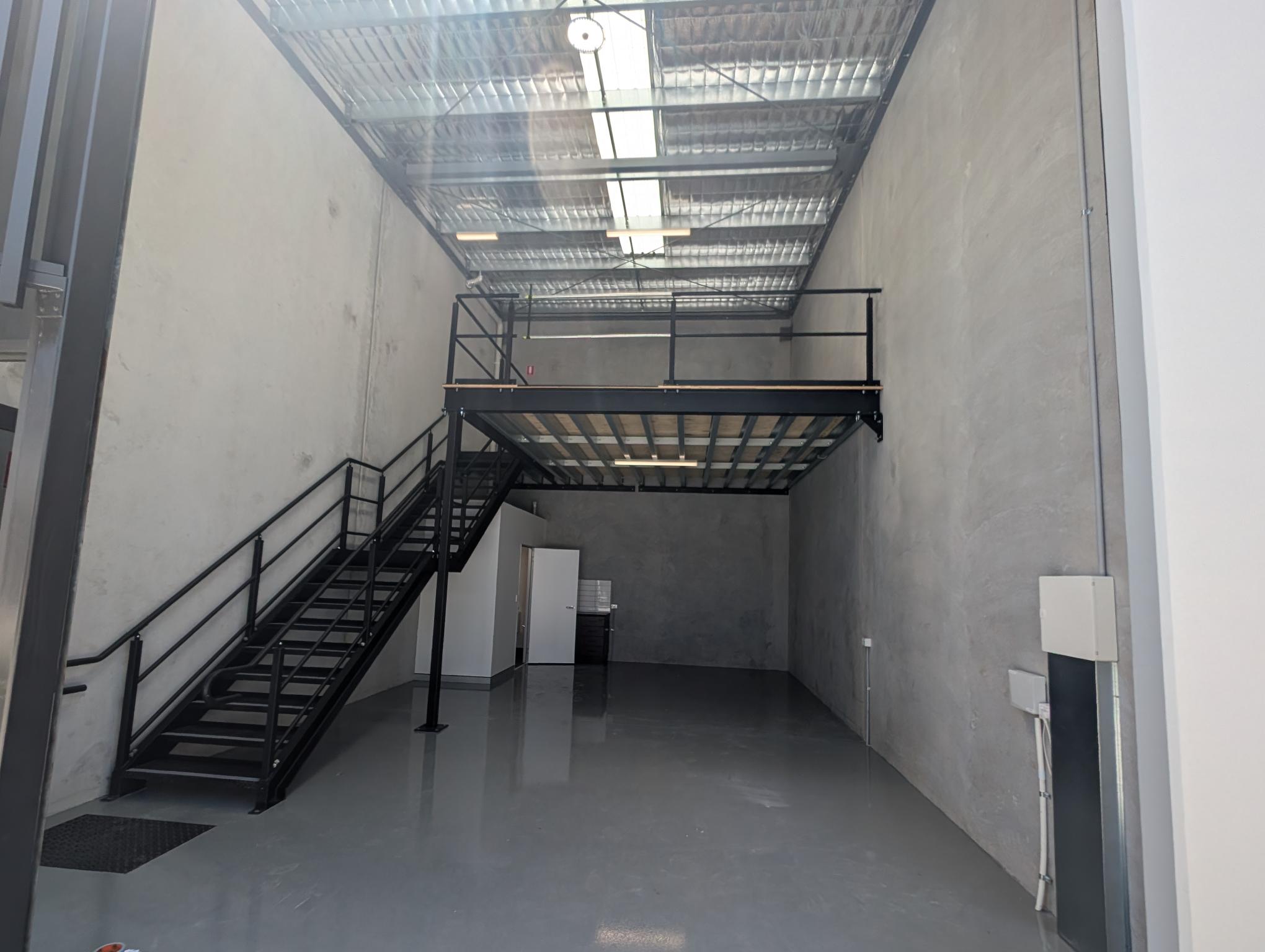
Green Design, Somersby NSW
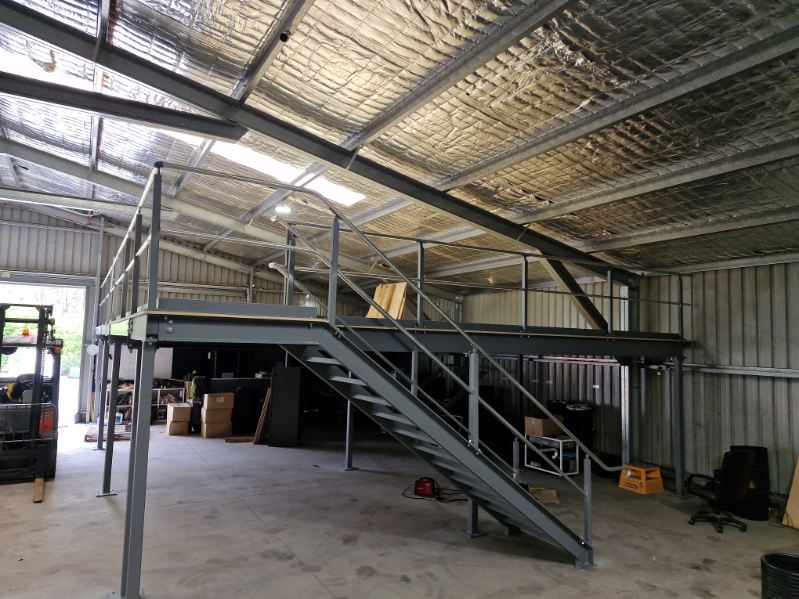
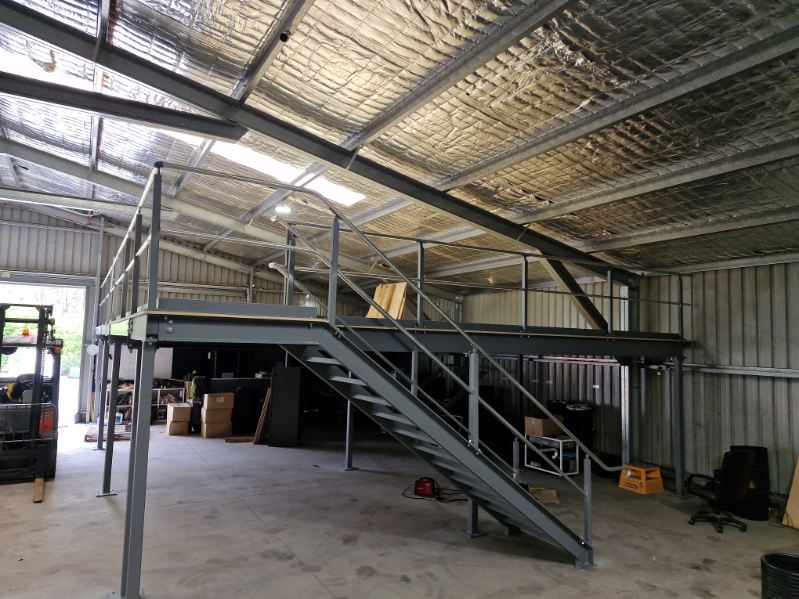
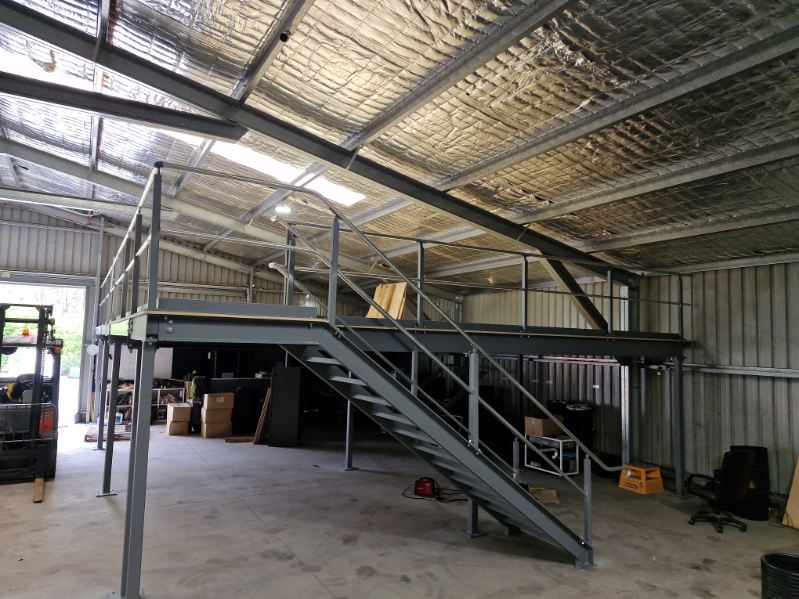
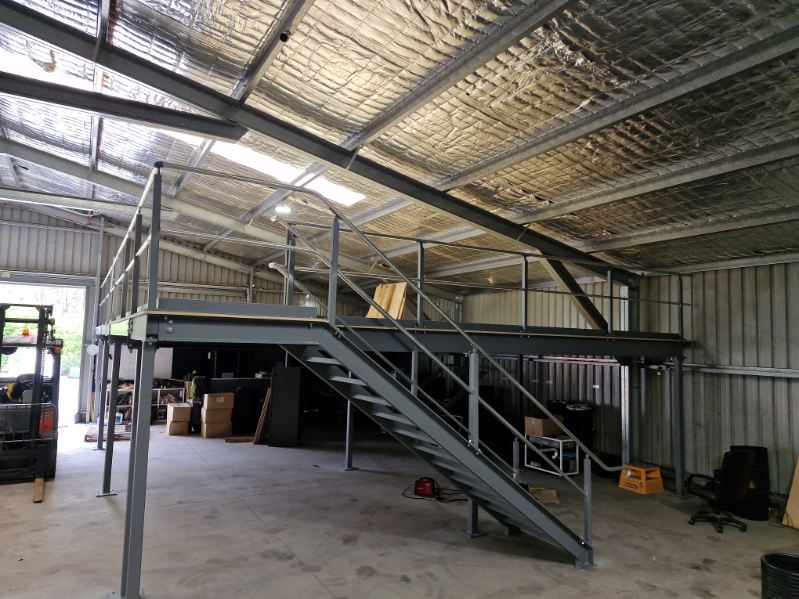
Sydney Composite Solutions, Brookvale NSW
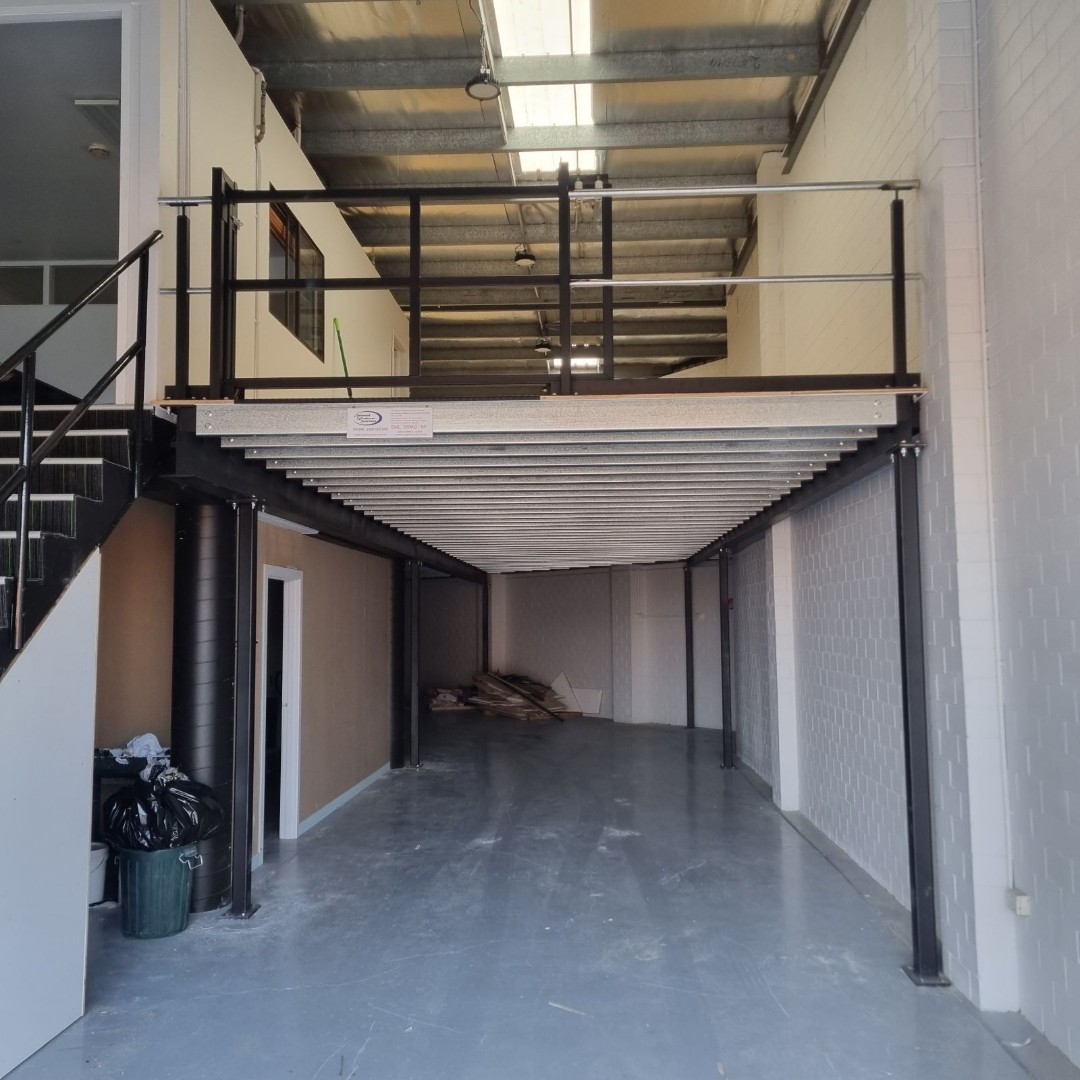
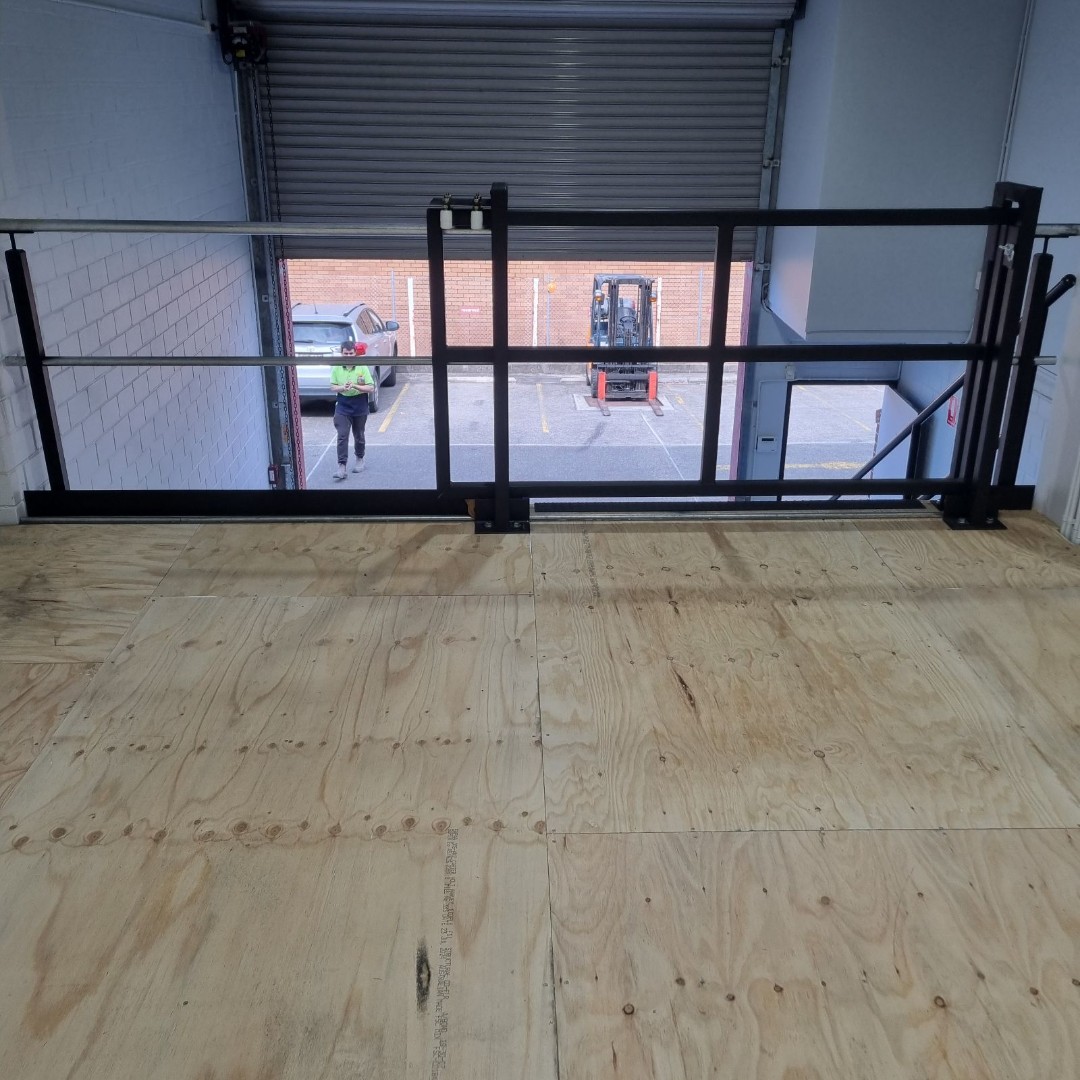
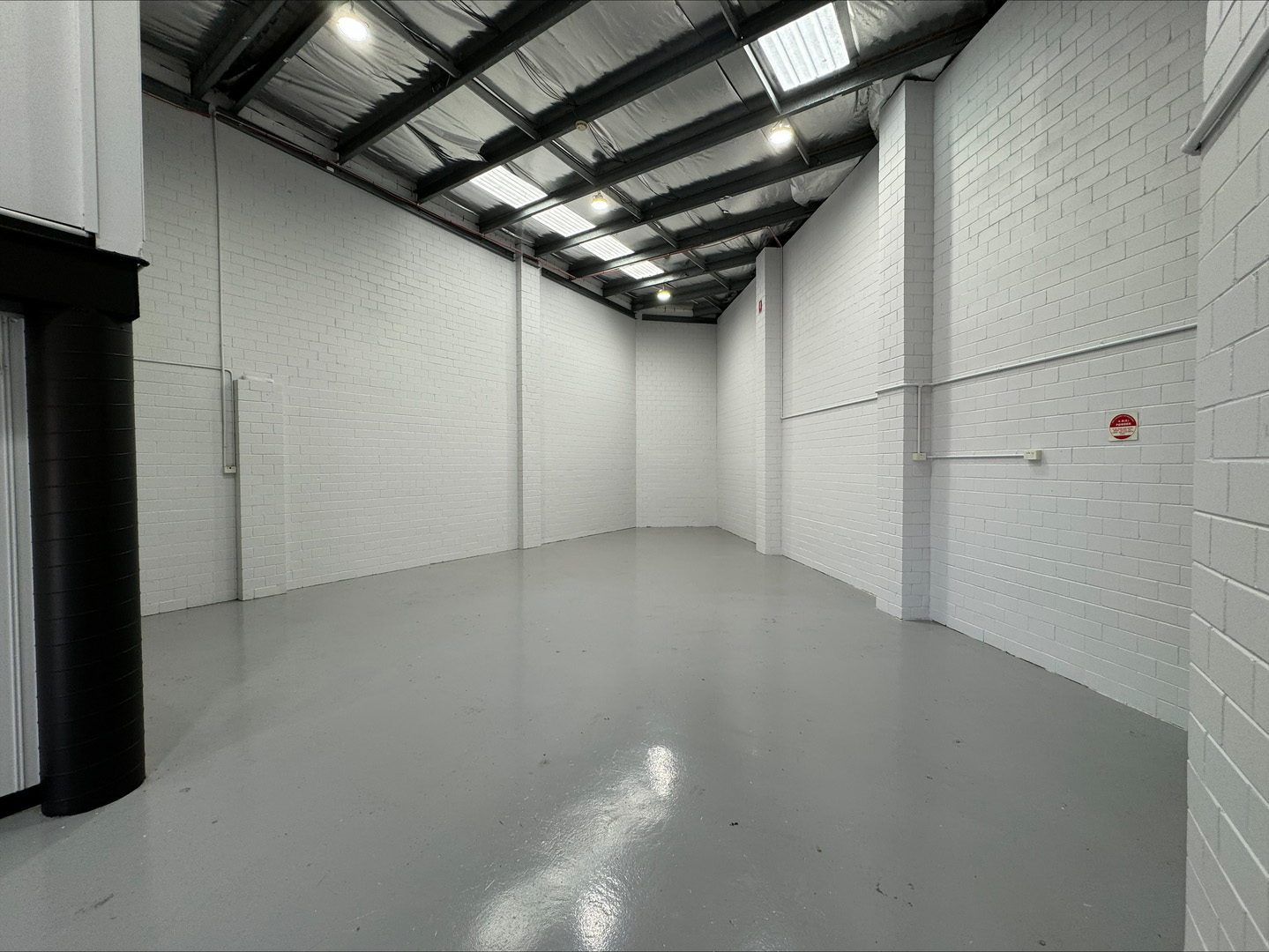

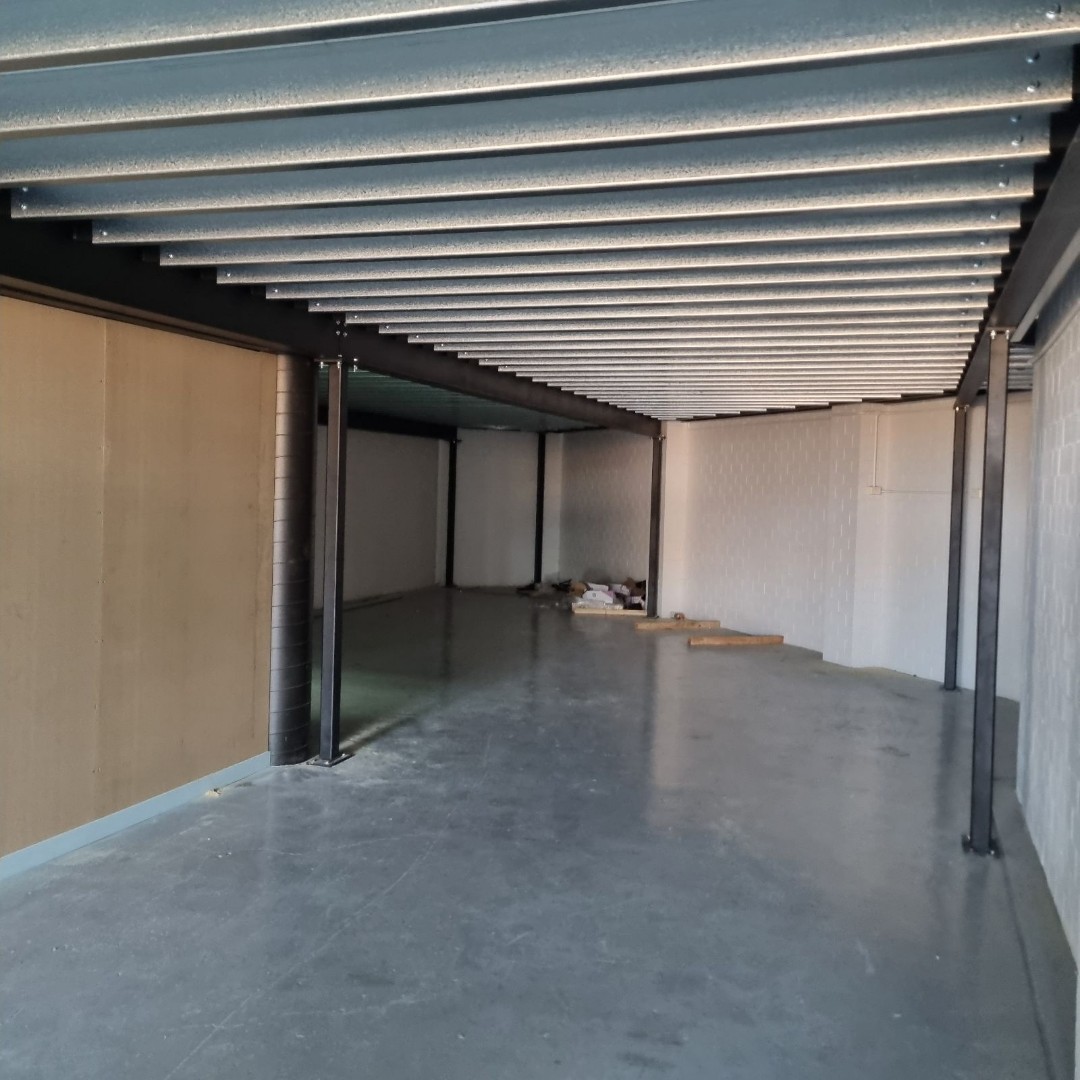
Austek Play, Morisset NSW
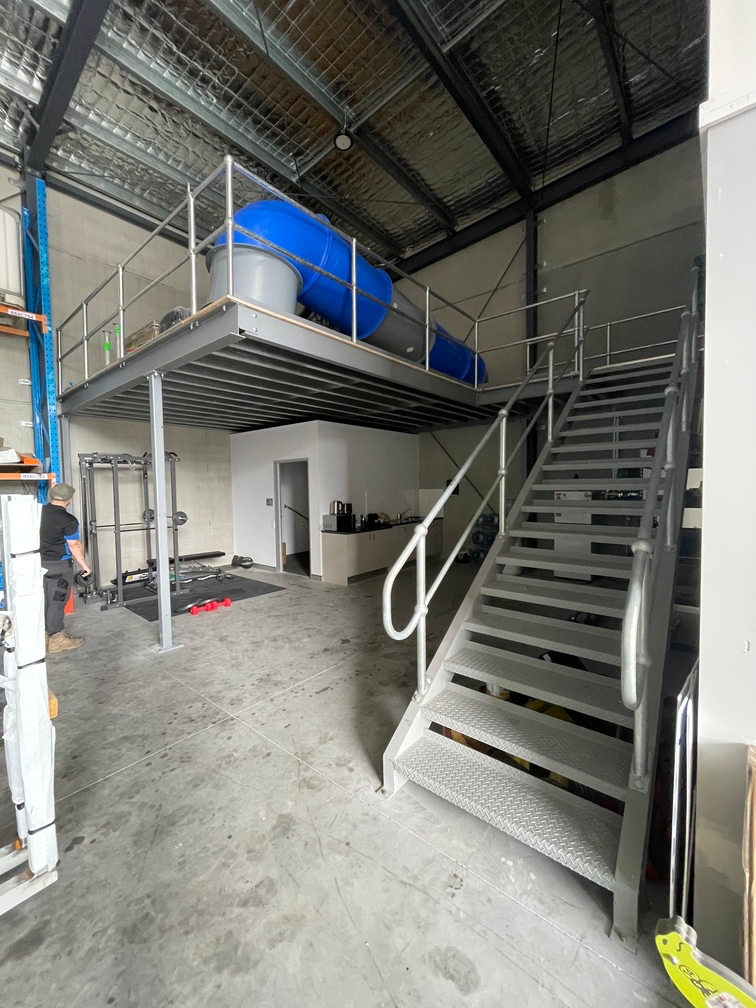
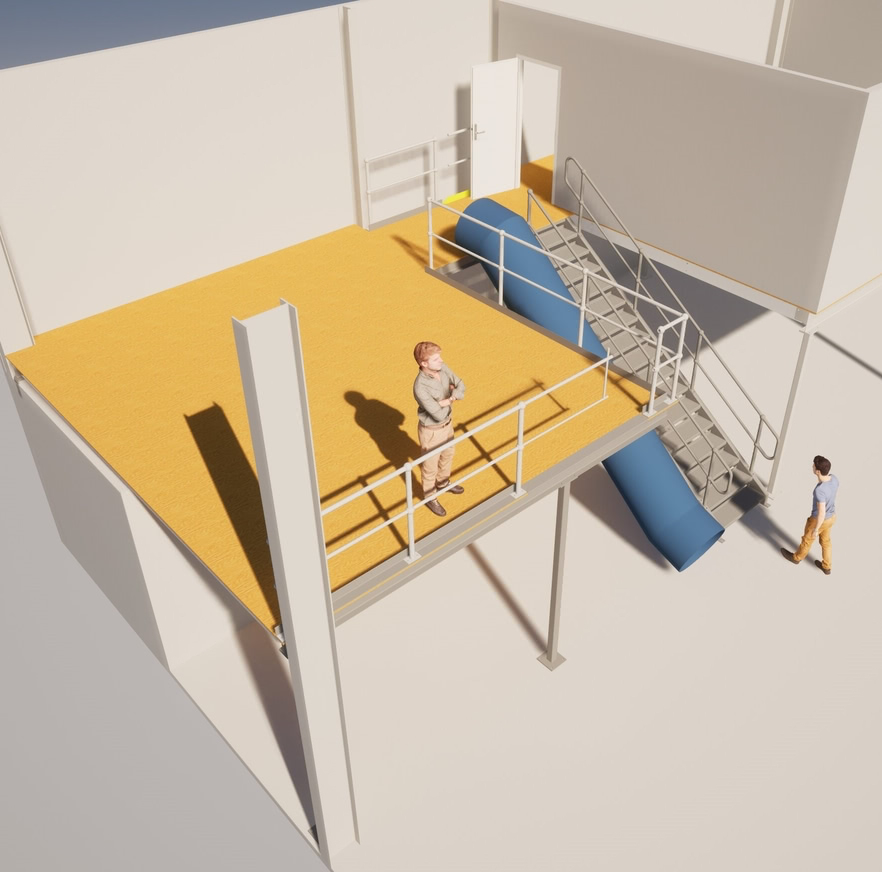
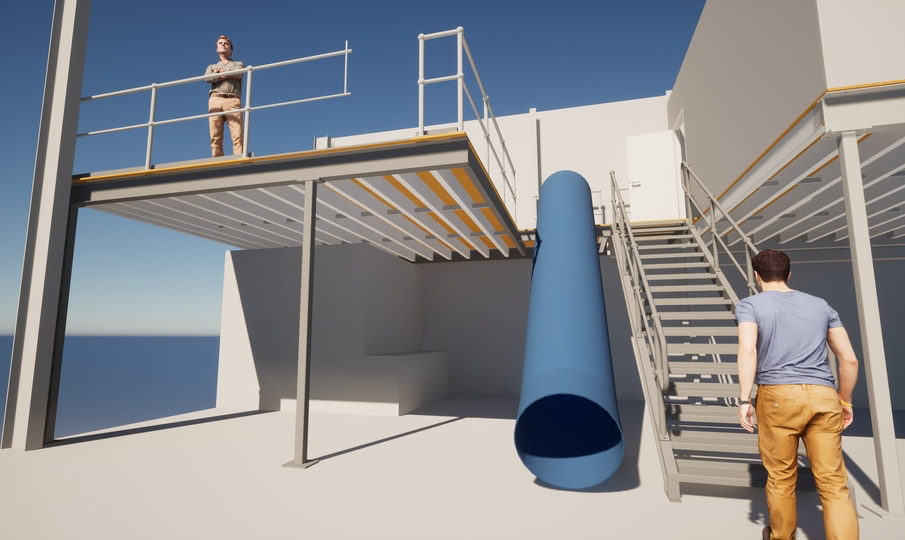
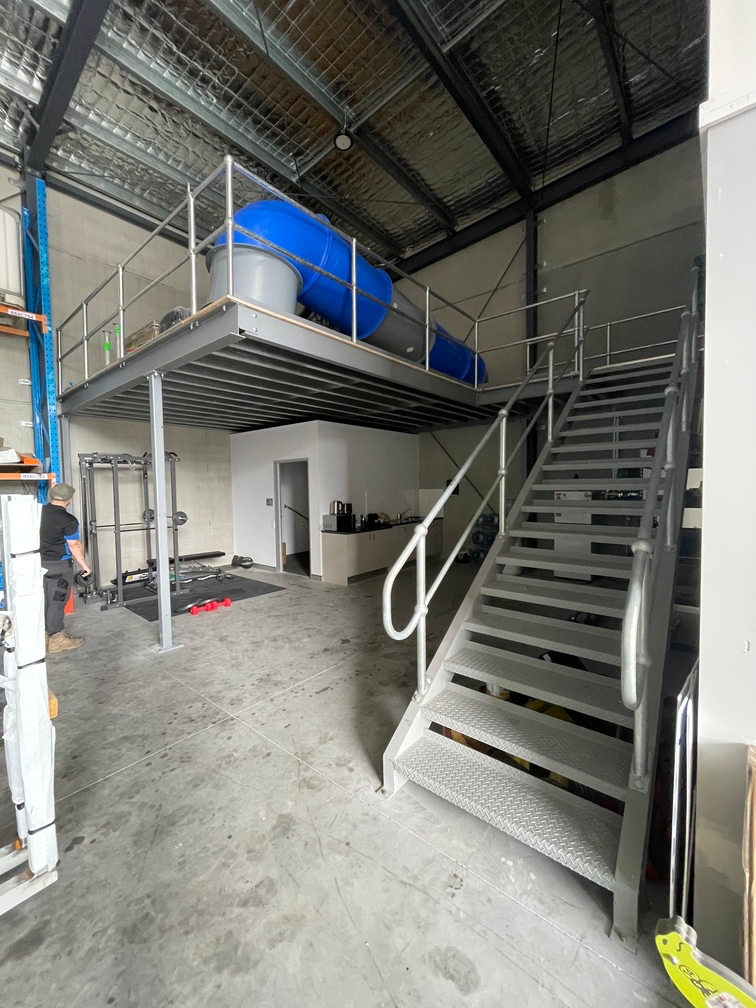
Modern Frameless Glass, Taren Point NSW
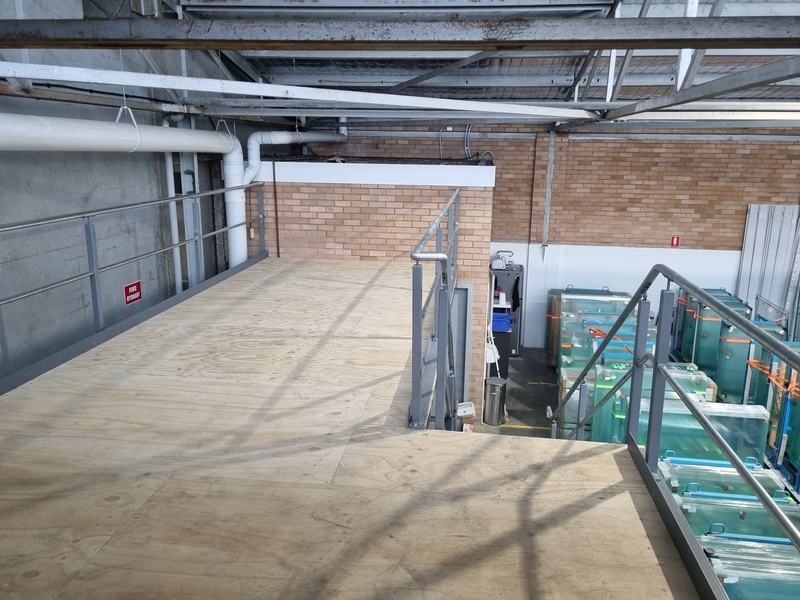
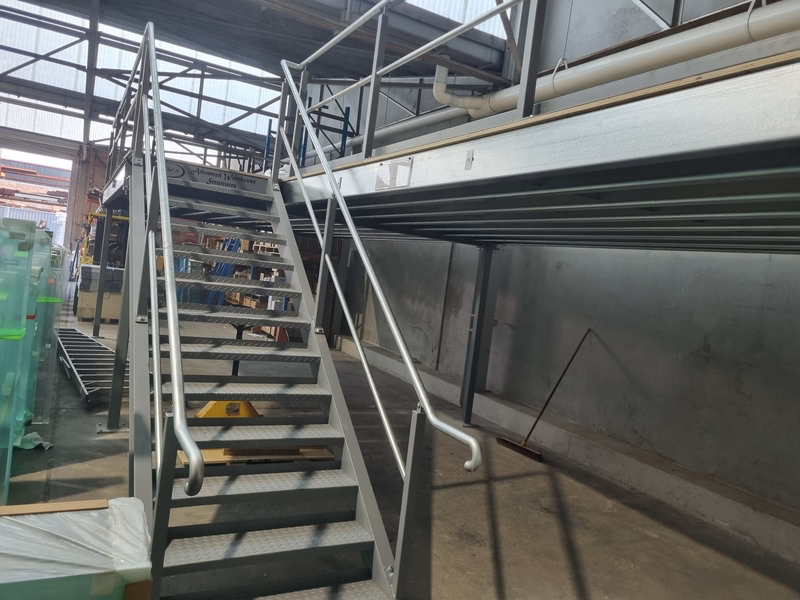

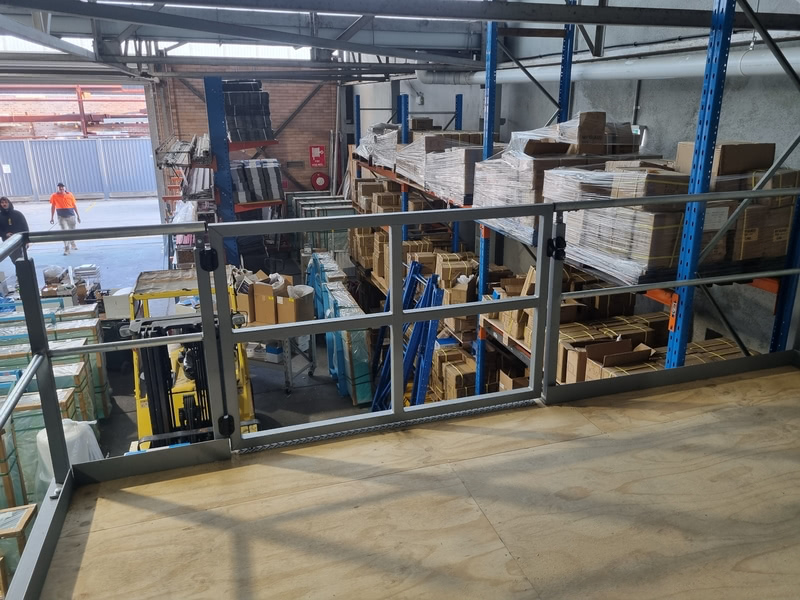
The Marshmallow Co, Wyong NSW
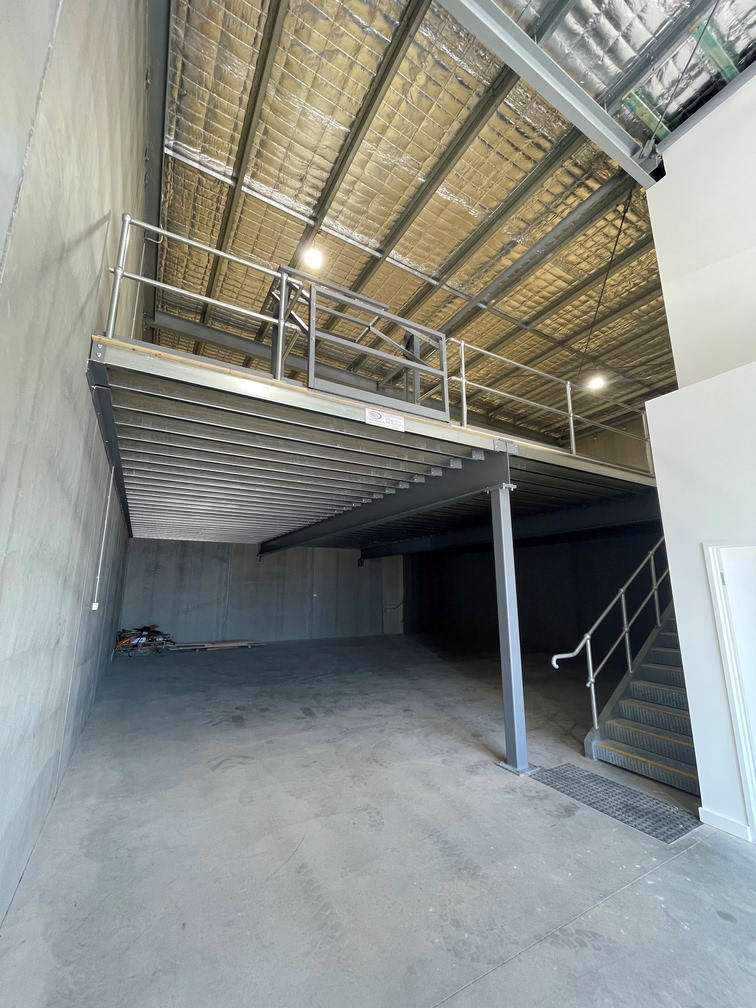
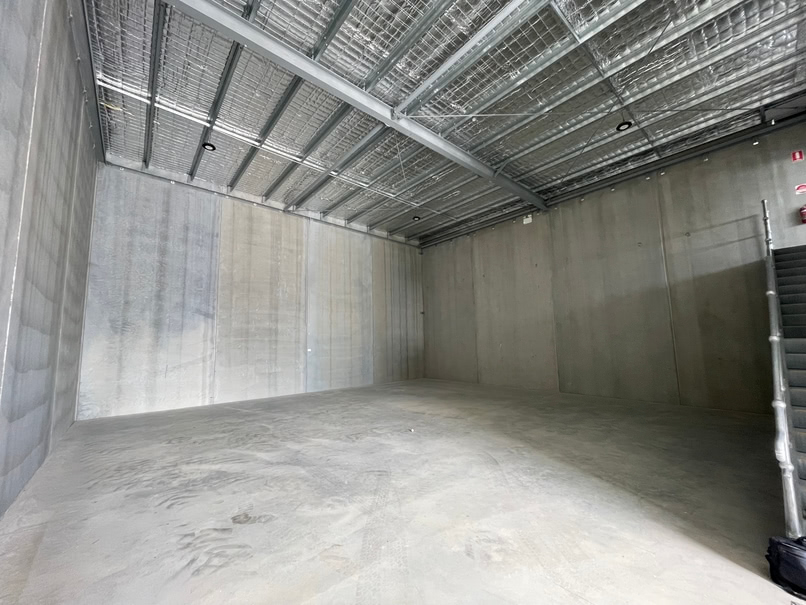
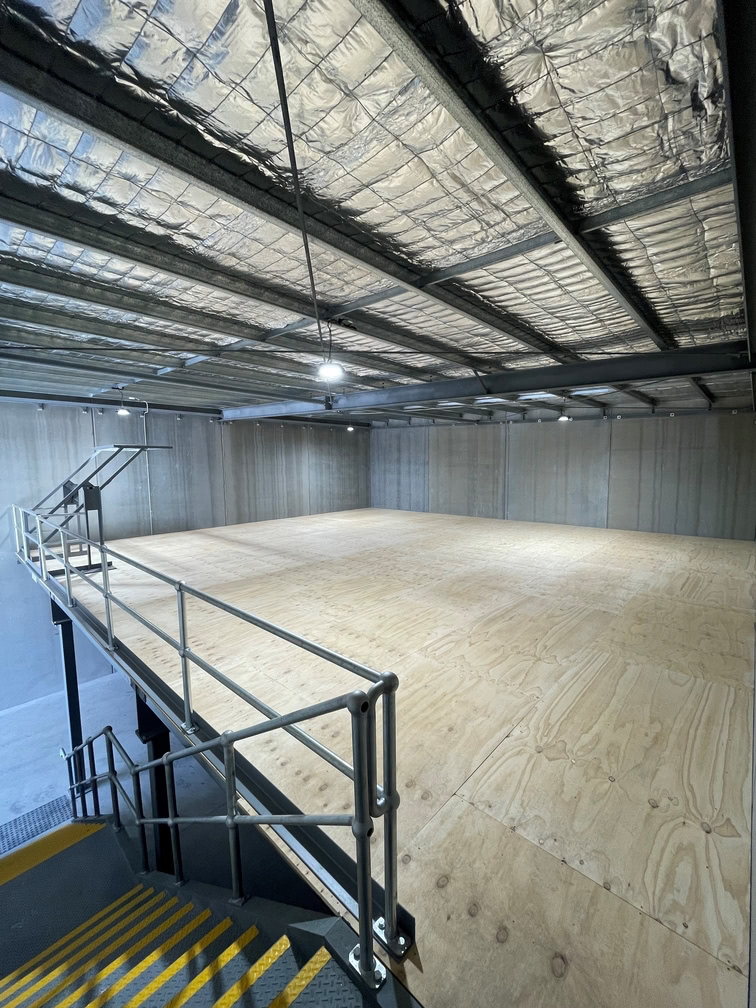
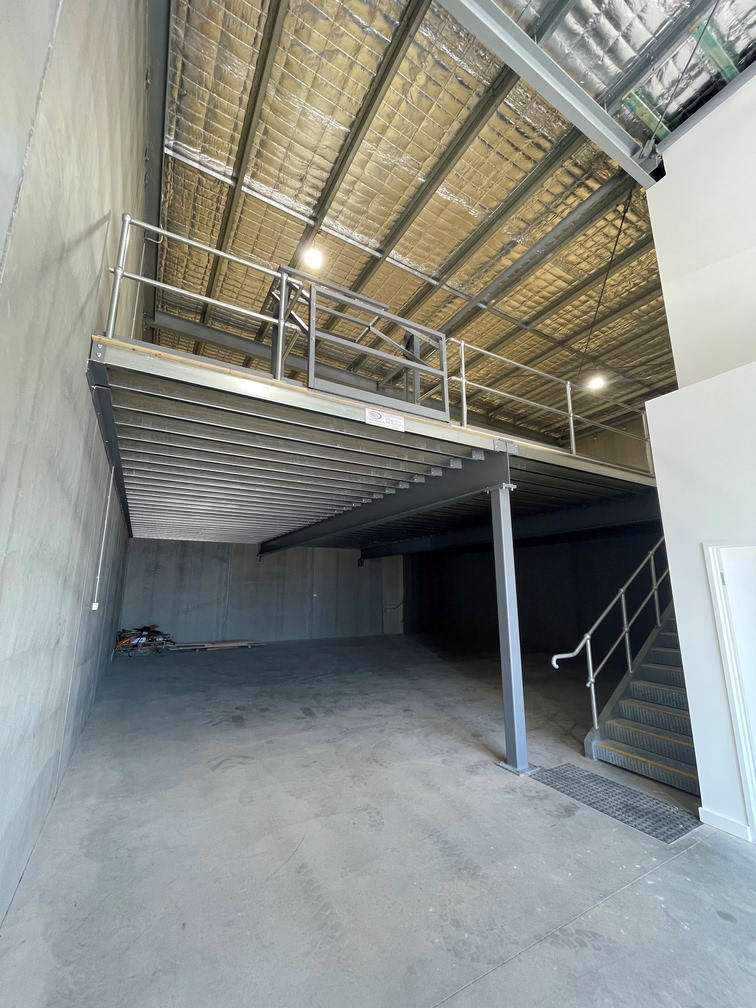
Louis Reos, Gold Coast QLD
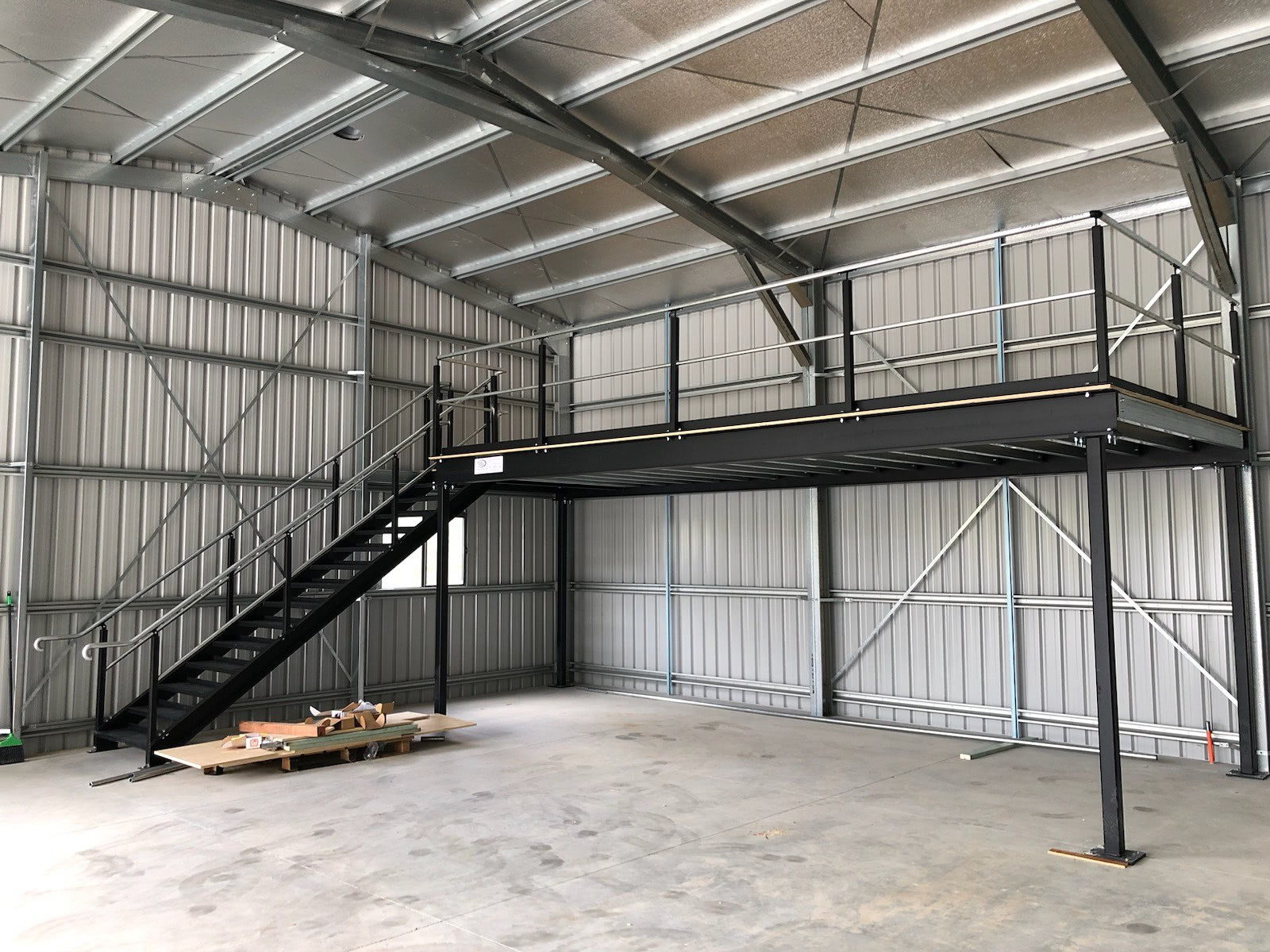
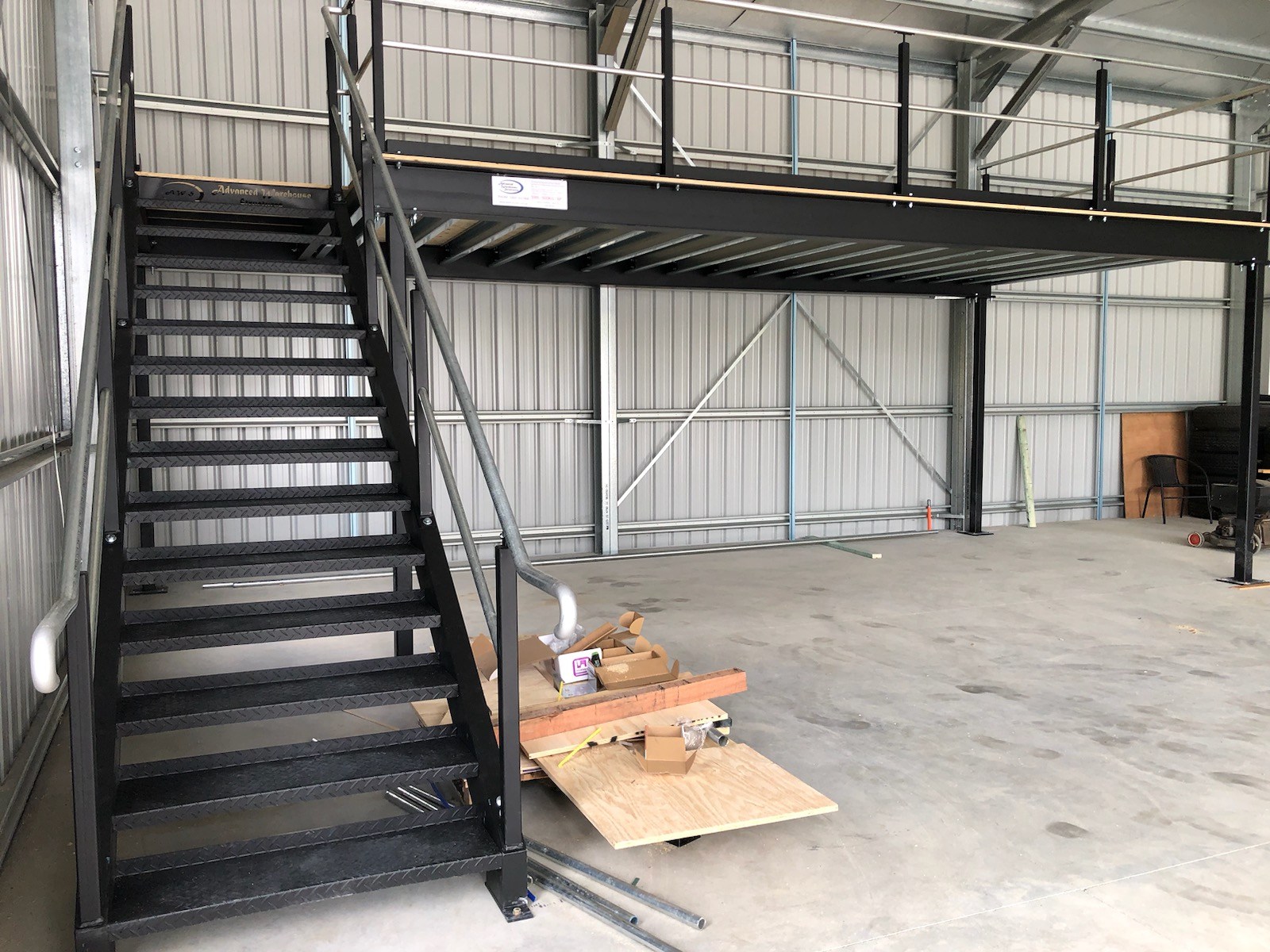
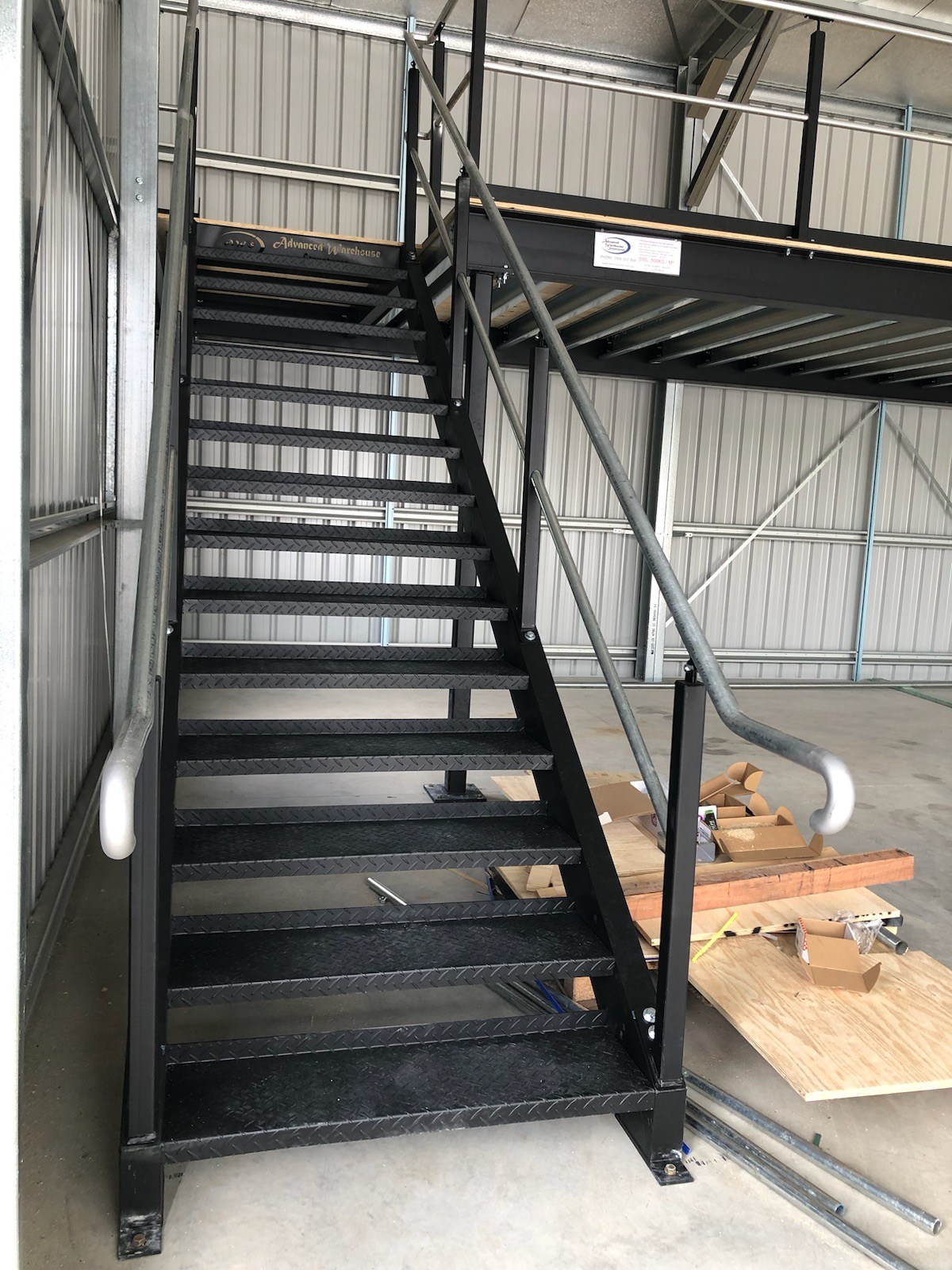
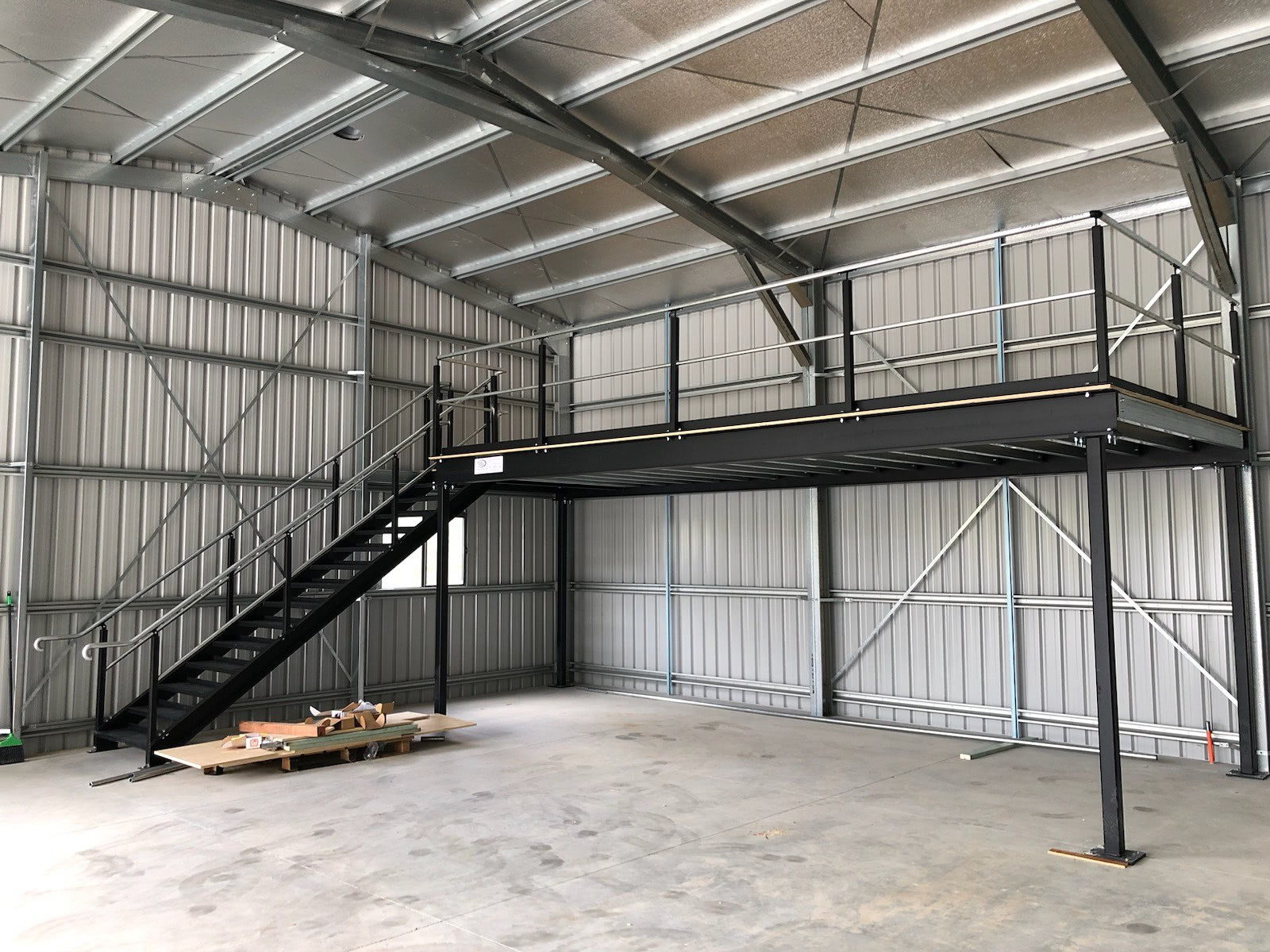
DPOB, Coolum Beach QLD
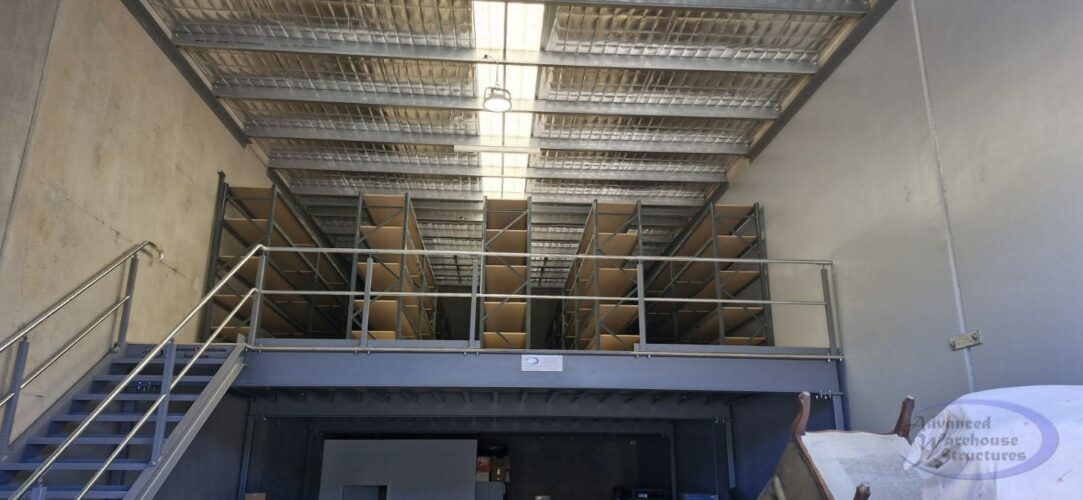
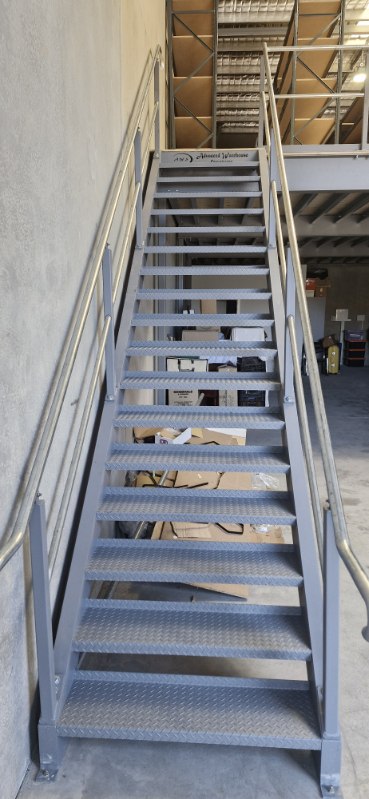
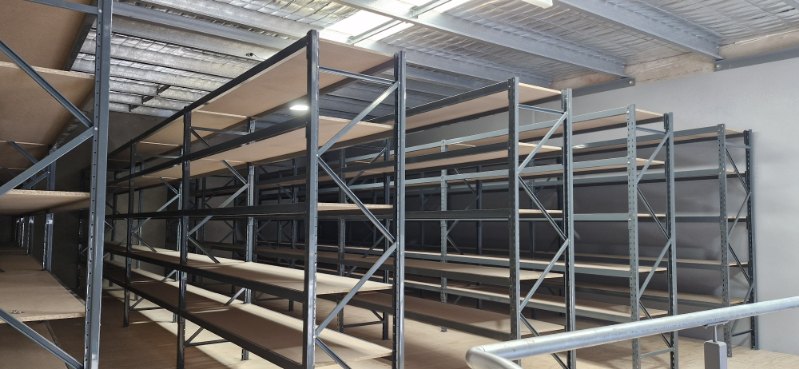
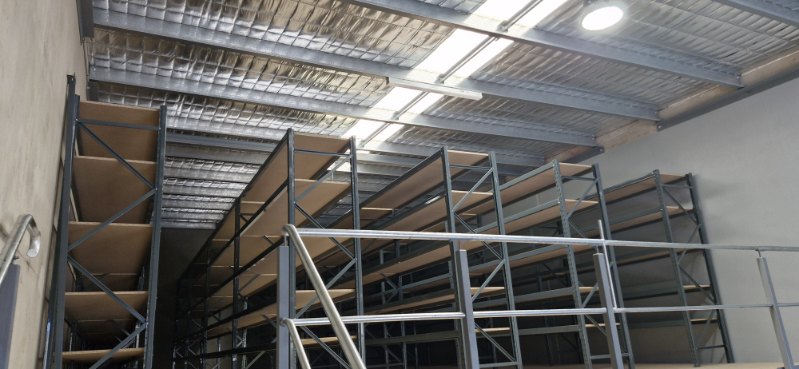
Mezzanine Floor For Honda Australia at Melbourne Airport
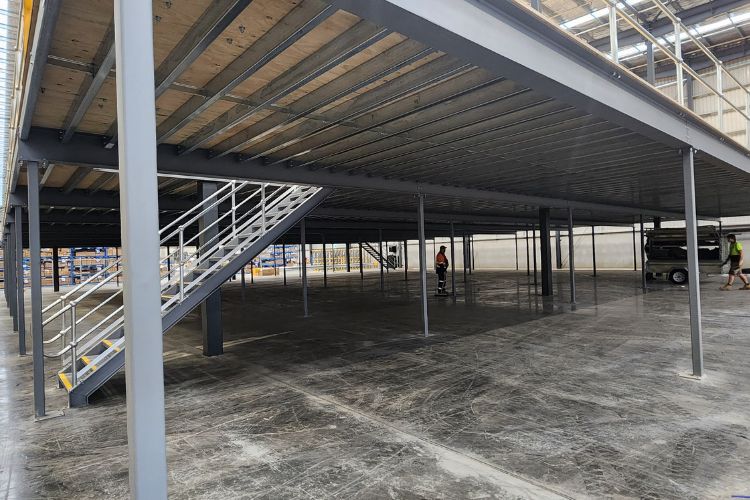
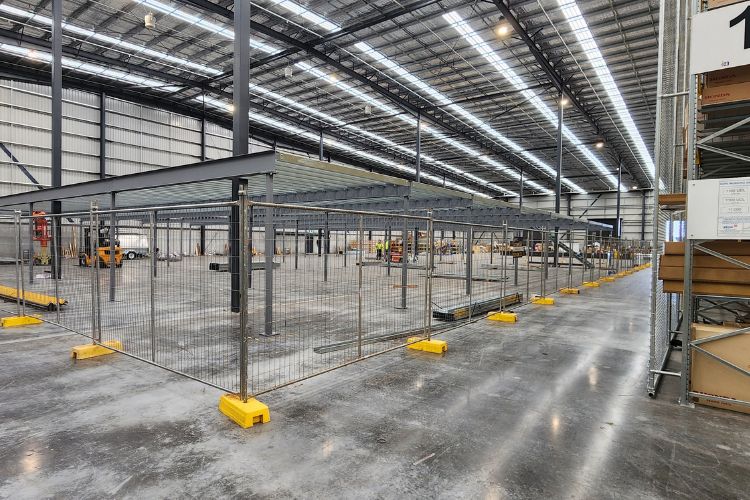
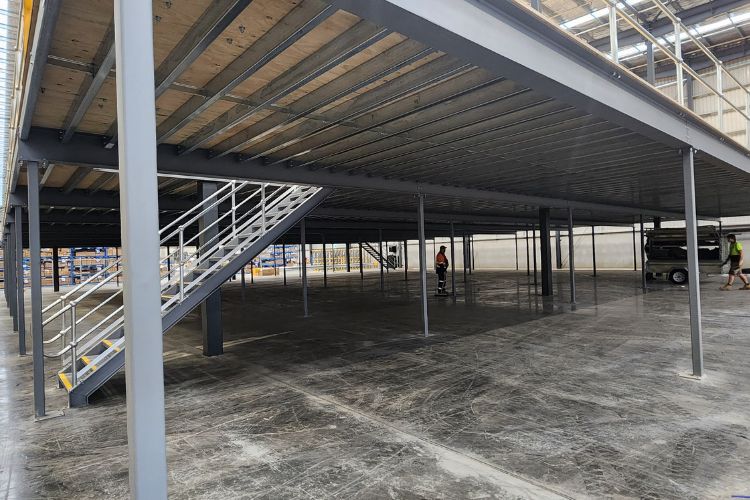
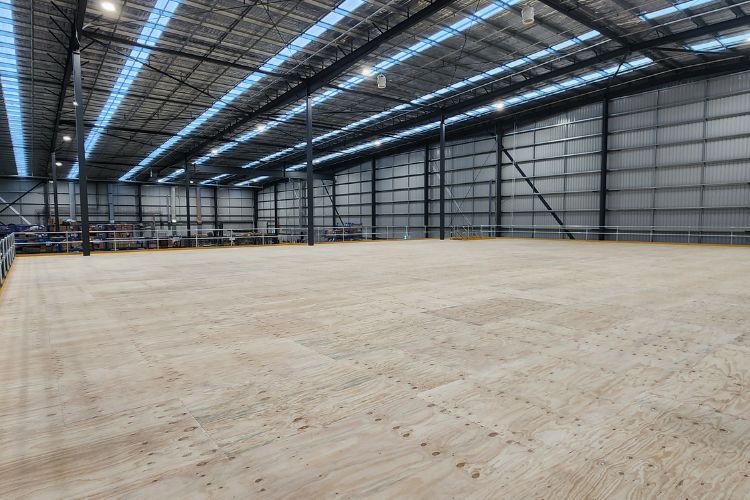
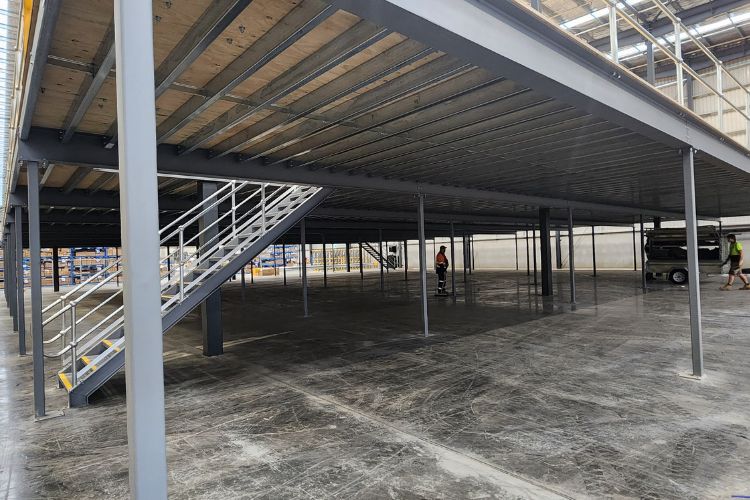
ConnectAbility Mezzanine Floor
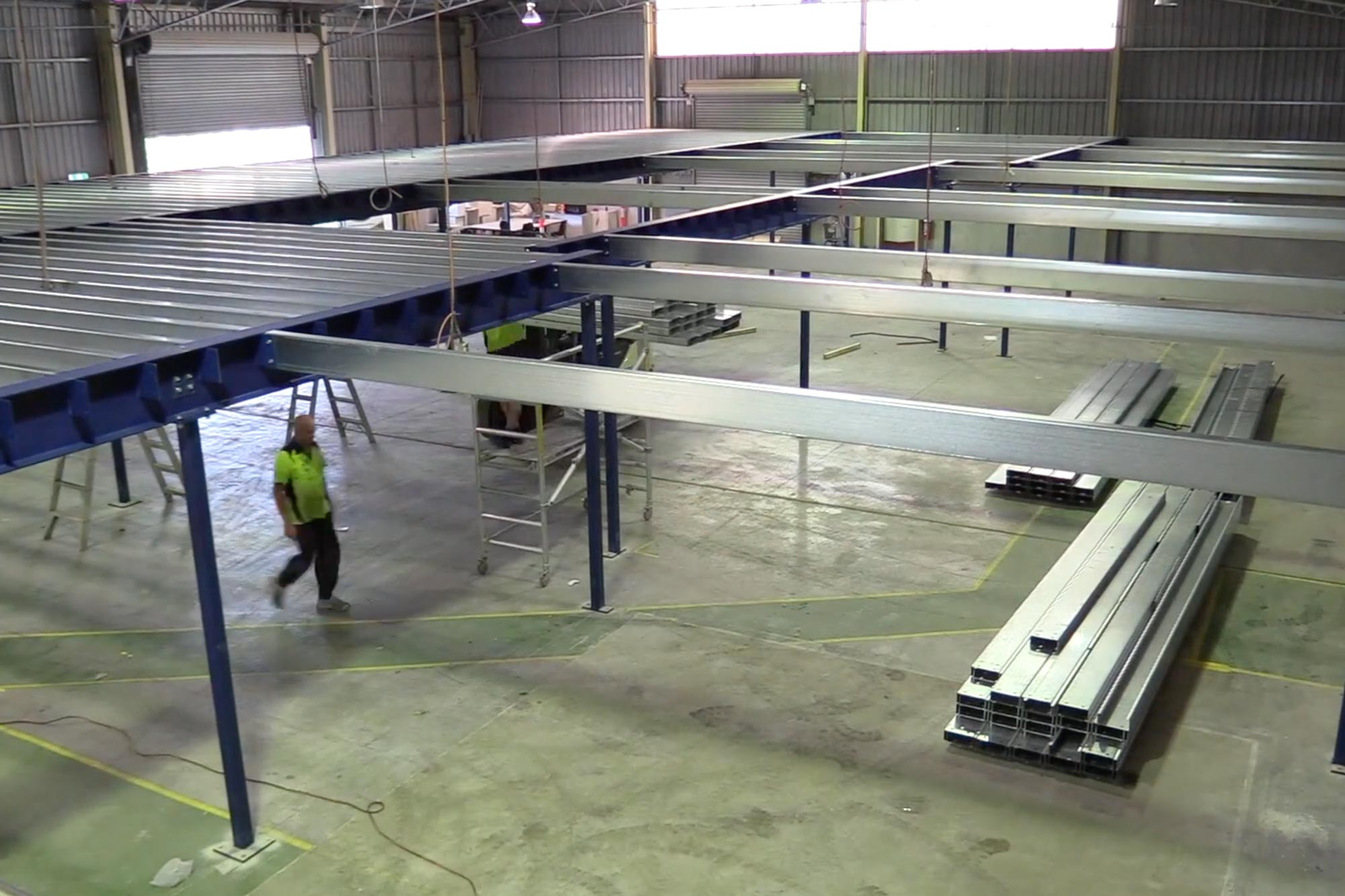
Waterlogic Structural Floor
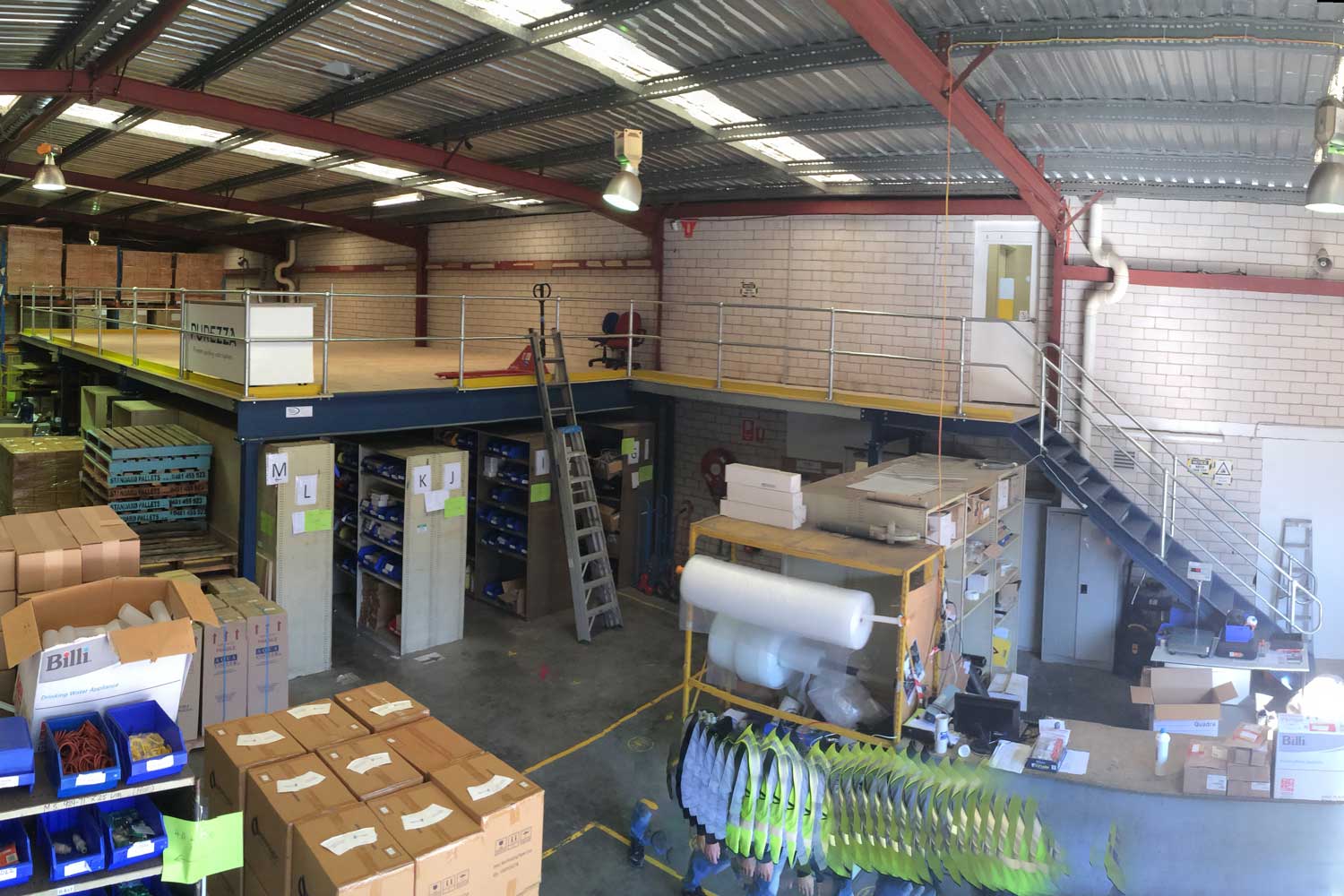
Huge Mezzanine Floor Completed In Wetherill Park
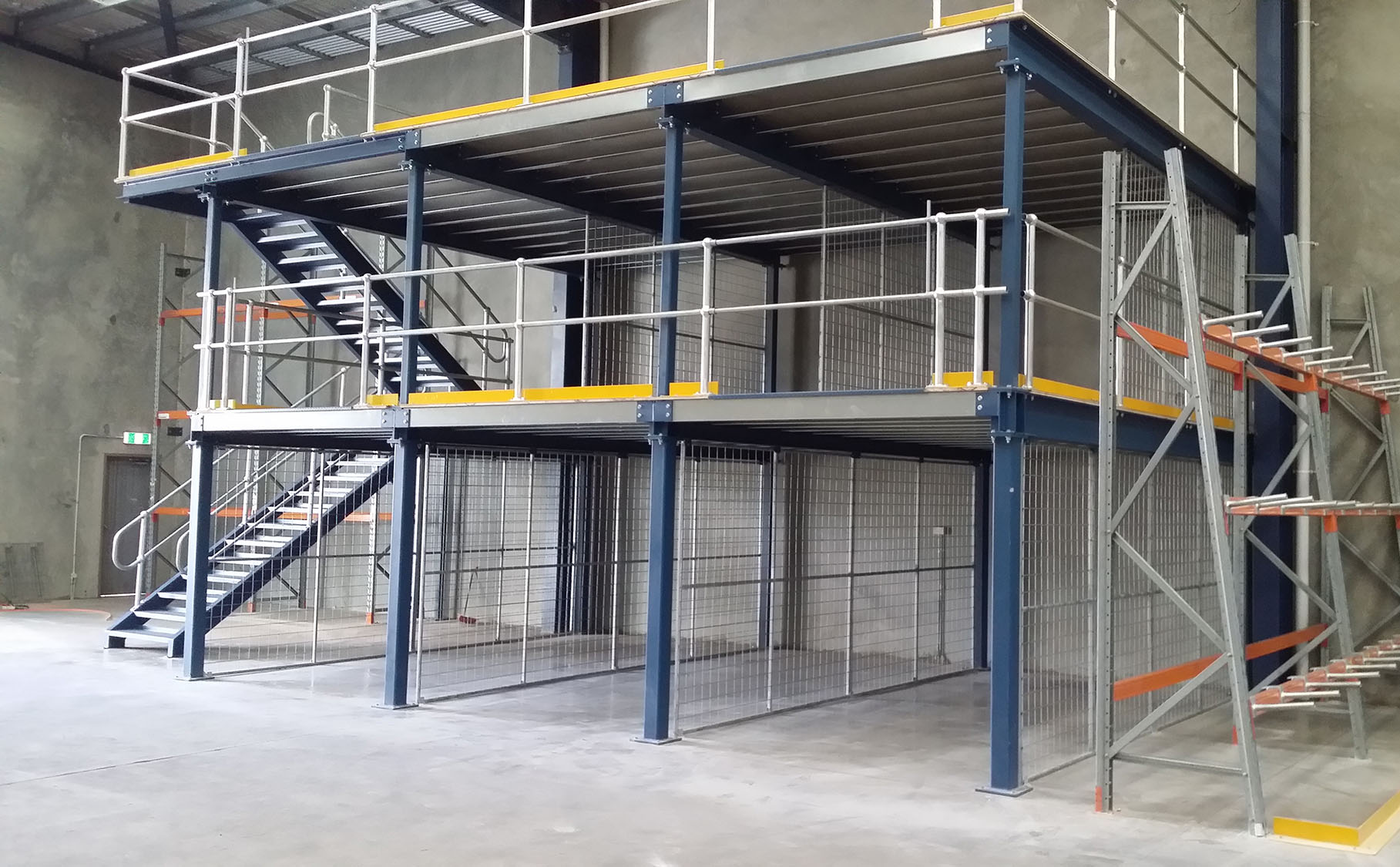
Shelving
DPOB, Coolum Beach QLD
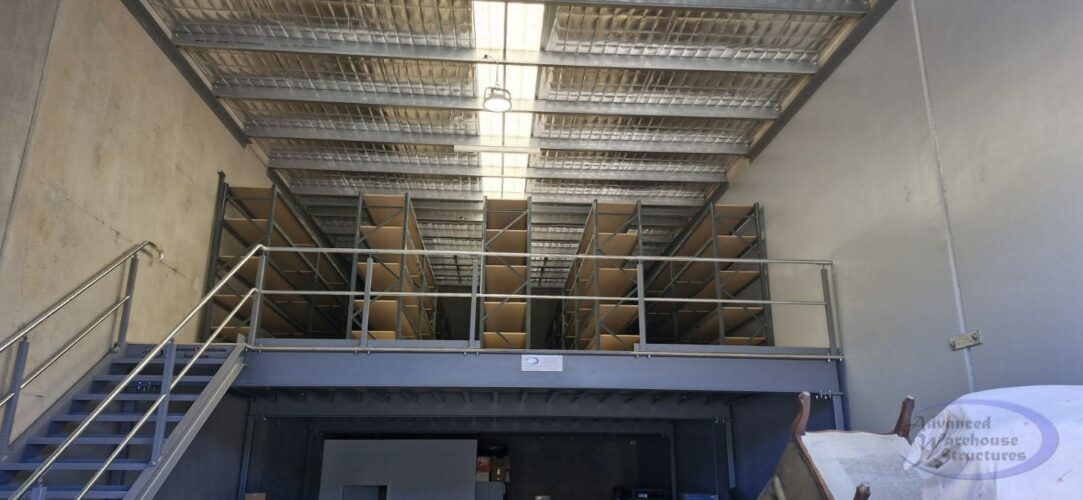
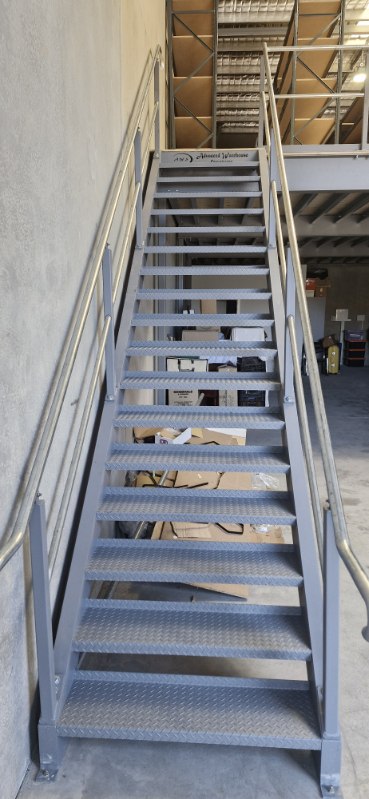
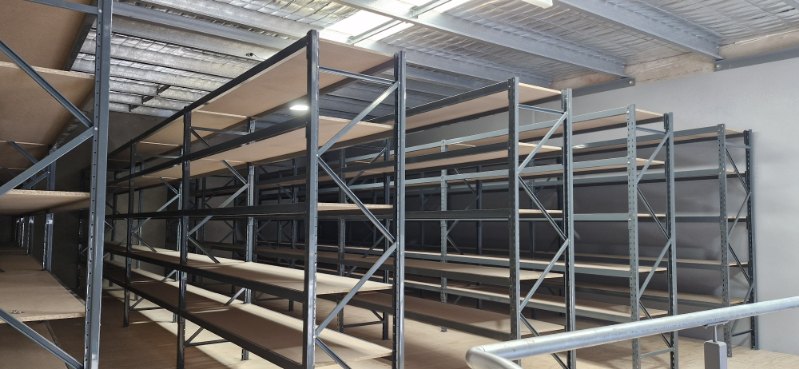
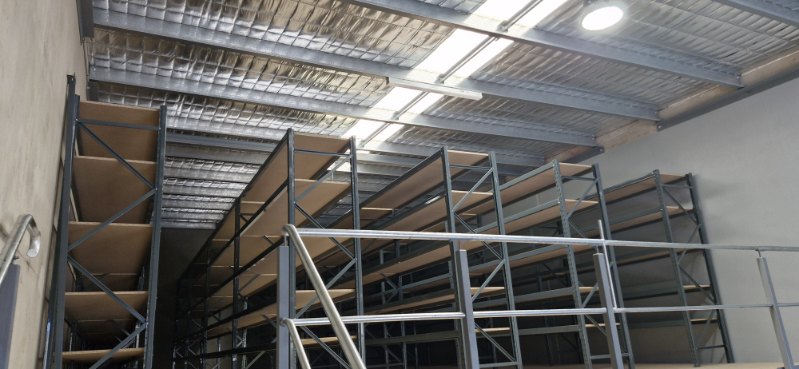
Pallet Racking
Beiersdorf Warehouse Relocation & Racking
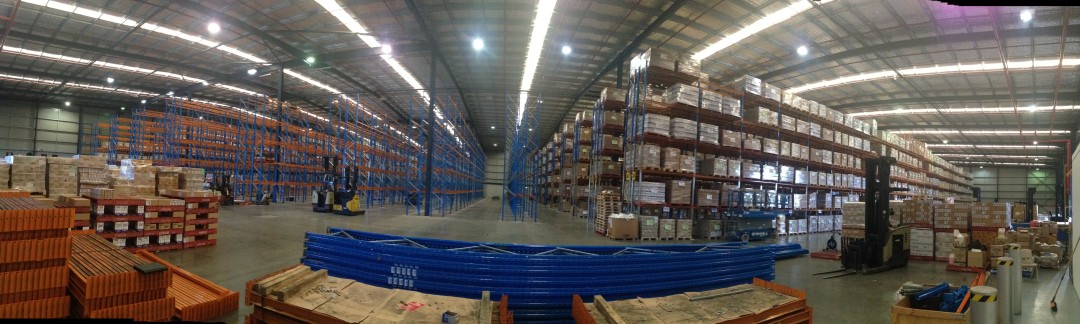
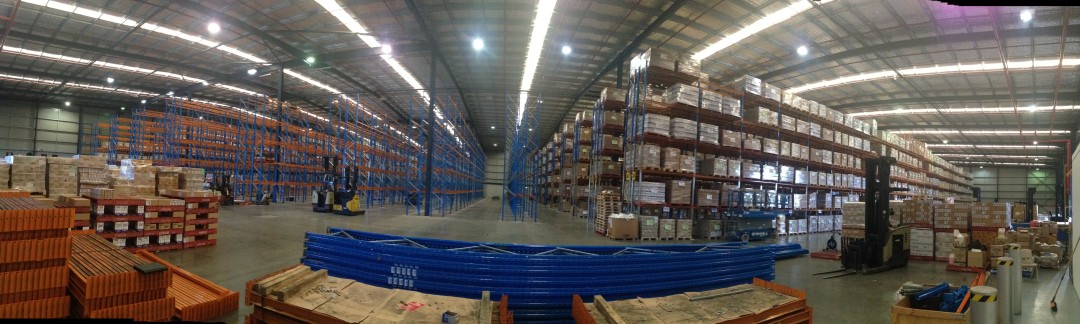
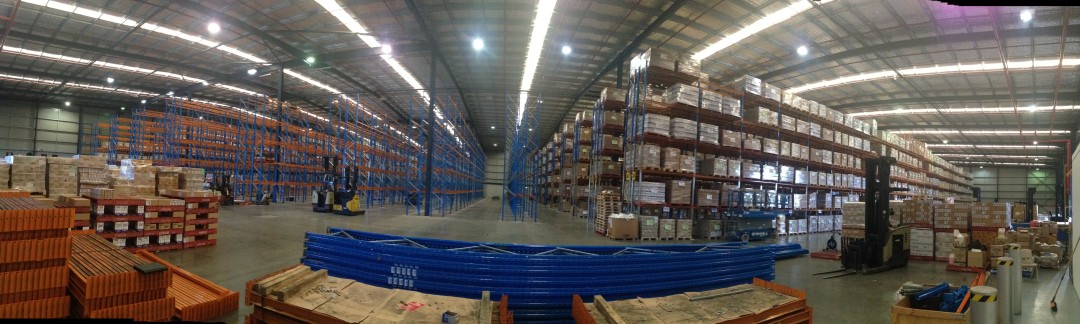
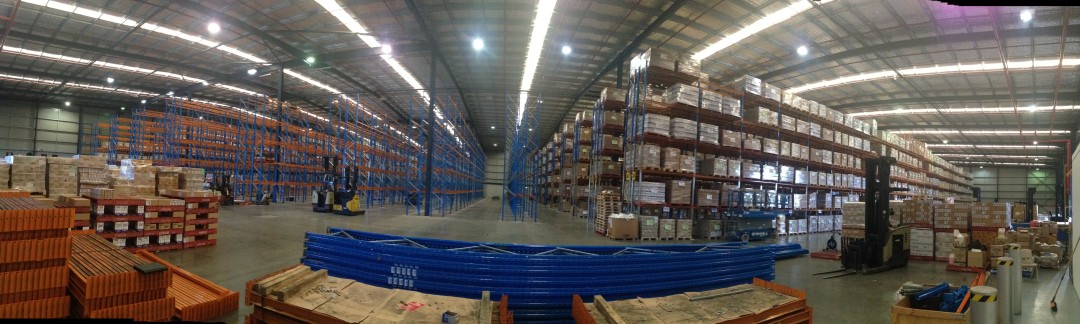