Warehouse Automation Guide
Constant advancements in warehousing have made automation technologies essential to many businesses.
Many warehouse automation solutions are available, but how do you determine the best equipment and hardware to meet your requirements? How should you go about implementation? Which existing operations should you target first?
Automation can noticeably impact your operation, whether you want to track inventory levels, improve quality control, reduce injuries, or better meet your business's and customers' demands.
Before automating your warehouse, you need suitable warehouse shelving and racking solutions in place. That’s where we can help. Let’s explore the types of warehouse automation available, their associated benefits, and why having the correct structures will set you up for success.
What is Warehouse Automation?
Warehouse automation involves using technology to streamline warehouse operations and improve overall efficiency. It is rising in popularity due to its potential to increase productivity, decrease manual mistakes, and improve customer satisfaction.
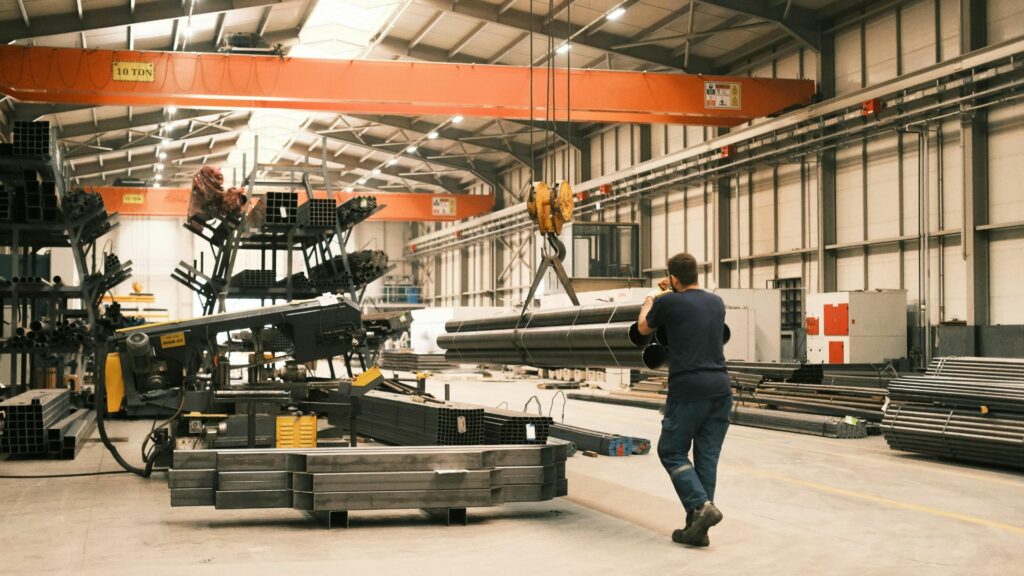
Warehouses automate their operations in various ways, including using software for data and warehouse robots to complete repetitive tasks. It can also help employees work smarter when sorting, tracking, picking, and packing orders.
Types of Warehouse Automation
1. Automated Storage and Retrieval Systems (AS/RS)
AS/RS are logistical solutions for improving picking processes and boosting efficiency and accuracy. They can be used for various operations, including sorting and packing items. The design effectively uses vertical space and can help increase storage density.
Some of the key benefits of the integration of AS/RS include:
- Lower labour costs
- Better product security
- Better ergonomics and safety throughout the working environment
- Improved order-picking accuracy
2. Conveyor Systems
A conveyor system is an automated means to transport goods from one location to another. Common components of a conveyor system include belts, wheels, rollers, and chains.
This machinery increases movement speed, reduces labour costs, and reduces the risk of injury to workers. Conveyor systems are especially useful for moving large quantities of heavy products from one set location to another. If there is a set pattern that products need to travel, a conveyor system is a great solution.
3. Warehouse Management Systems (WMS)
A warehouse management system is a software application that helps your business with everyday operations. A WMS creates a centralised means of tracking shipping, inventory analysis, and stock locations throughout your warehouse. This system can greatly improve overall management, providing easy-to-access and accurate data.
A common issue for warehouses without a WMS is that the incorrect amount of stock is ordered due to inaccurate information. A management system allows you to monitor resources and stock levels and avoid these issues.
A good WMS also allows you to track orders, receive accurate data analytics, better complete order fulfilment, and monitor customer information and order status. When well implemented, a WMS reduces product wastage, improves productivity and inventory movement, and reduces the challenges of inaccurate data.
4. Robotics, Software and AI
Warehouse automation thrives when applied to repeated tasks, allowing your employees to focus on creative solutions.
Picking automation: Improves the entire picking process and greatly reduces the chance of human error.
Barcode scanners: Ideal for keeping track of orders and stock, improving data analysis and processing inventory.
Automatic guided vehicles: Forklifts, pallet jacks, and cranes are all mainstays in warehouse environments, but automation technology reduces labour costs and the risk of human worker injuries.
Back-office: Software can help with accounting, payroll, scheduling, and other admin duties.
Benefits of Warehouse Automation
1 - Increased efficiency
Warehouse automation can greatly improve your efficiency by automating repetitive warehouse tasks, reducing human error, and speeding up certain procedures. Tasks like finding storage locations and inventory tracking can be done instantaneously by artificial intelligence, speeding up the packing process for your workers.
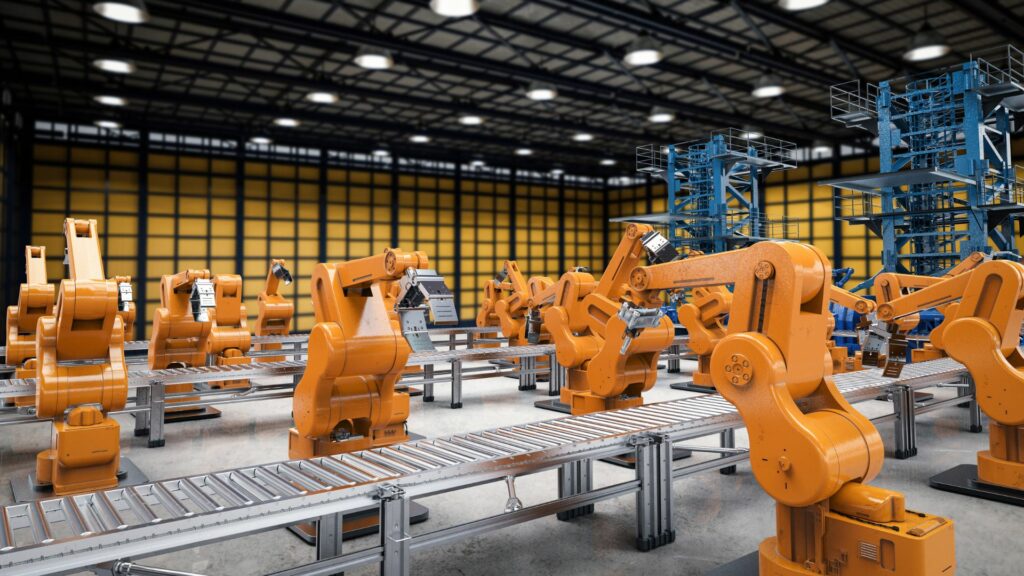
2 - Enhanced accuracy
Even small errors in tracking inventory can be expensive, slow productivity, and cause downtime for your supply chain. Technologies such as a WMS centralise inventory management and make data easier to use for inventory control, order picking, and similar aspects of your business.
3 - Cost savings
Warehouse automation systems reduce mistakes, maximise productivity, and improve workflows, all of which can cut down on labour costs and expenses caused by human error. Cutting down on mistakes and finding more consistency in performance will lead to less downtime and more long-term profitability.
4 - Improved safety
Warehouses are busy areas, and accidents can happen. Automation such as conveyor belts, AS/RS, and picking automation reduces heavy lifting and the chance of injury throughout your workforce.
Automation technology can reduce the chance of injuries, helping to protect your warehouse workers.
Good Warehouse Shelving and Racking for Warehouse Automation
Ensuring your warehouse is fitted with high-quality, reliable and structurally sound shelving and racking is essential for warehouse automation.
Accessibility: To minimise the need for intervention from you or your workers, automated systems such as AS/RS and robotics for packing automation need to be able to move around your warehouse repetitively and without obstruction.
Our selective pallet racking can store a large number of items and allows 100% accessibility to every pallet, meaning your new systems can work to complete tasks quickly and efficiently.
Flexible design: Our mezzanine floors are easily movable and customisable. This flexibility allows your structures to grow and evolve over time in line with the introduction of new or changing warehouse automation technology.
Durable structures: Facing downtime in any part of business can be detrimental to success, but when it impacts automated processes too, it can lead to further expenses or difficulties like missed or incorrect orders.
AWS provides structures you can rely on. We bring over 125 years of collective experience and take pride in ensuring all our projects and installations are completed to the highest standards to ensure your warehouse structures don’t impact on the effectiveness of your automated systems.
Best Practices for Implementing Warehouse Automation
1. Assessing your needs
The first step businesses need to take is to consider their current operations and determine where there is room for improvement. Do you have issues with inventory loss or accuracy in your work environment?
Are products being manually moved along the same route repeatedly? Are there any repetitive tasks taking up human workers' valuable time? Does your warehouse have the appropriate structures in place to facilitate automation?
Identifying the issues you must resolve is the first and most important step in finding a solution. Considering these factors will play a huge role in optimising your warehouse.
2. Choosing the right technology
No two warehouses are quite the same, so methods that work for another business may not be ideal for you. Once you know the issue you need to resolve, you need to find technologies that fit within your budget and will best improve your overall business goals. The right automation system is key in planning the upgrading of your warehouse.
3. Employee training for productivity
Technology can improve warehouse processes, but human intervention is still required to maximise your investment. Training your warehouse employees is, therefore, a necessity. Frequent employee training, both on how to use the systems and on any safety protocol, will ensure efficiency and safety throughout your warehouse space.
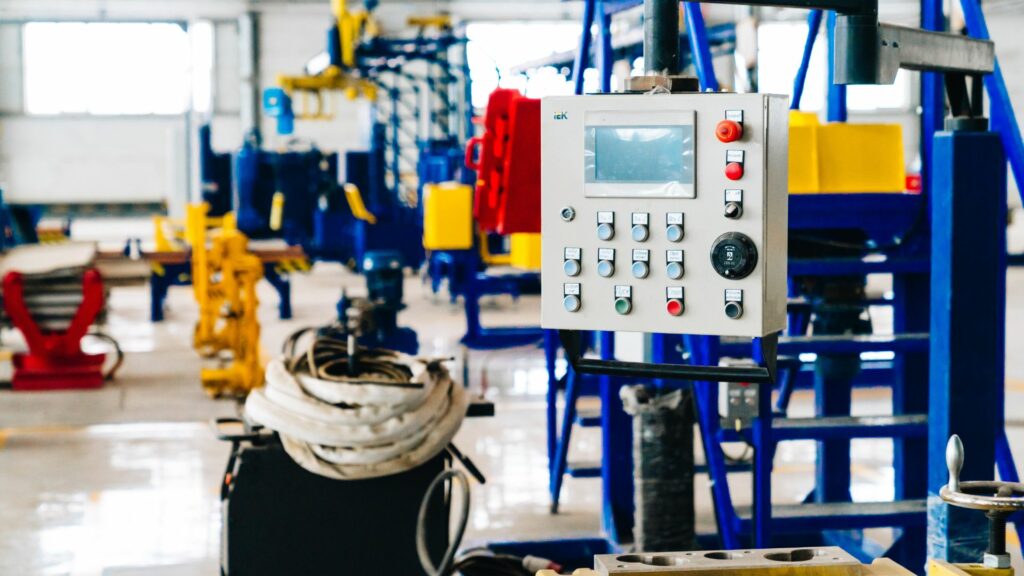
Teaching warehouse workers about necessary maintenance will ensure machines are kept in top condition and reduce downtime and safety issues.
4. Continuous improvement
With technology constantly evolving, it's important to be willing to review and update your automation strategy over time. The key to growth and improvements in your warehouse is to review constantly. Look at performance indicators, listen to your warehouse workers, and be open to new ideas. Being continually willing to improve means your business can adapt to new technologies and software solutions.
Choose Advanced Warehouse Structures to Ensure Your Warehouse is Ready for Automation
Need help ensuring your warehouse layouts and infrastructure are ready? We've designed, constructed, and installed mezzanines, warehouse shelving, and storage racks in various facilities and warehouses. We use only the highest quality materials and guarantee your final product will meet all industry and safety standards.
Want to take your mezzanine game to the next level? Contact our expert, friendly team today to discuss how to improve and upgrade your warehouse.
Advanced Warehouse Structures is Here to Help with Your Mezzanine and Shelving Needs!
Thinking about warehouse automation but want to make sure you have the correct structures in place first to ensure maximum success? Contact Advanced Warehouse Structures today for all your mezzanine, shelving and racking needs.